Гидроксид кальция: свойства и применение. Приготовление известкового молока.
Известь - вяжущий материал, получаемый путем высокотемпературного отжига (1000 -1200 о С) в шахтных или вращающихся печах осадочных горных пород состоящих преимущественно из карбоната кальция СаСО 3 (известняки, мел, доломит).
В зависимости от содержания в карбонатной породе примеси глины возможно получение или воздушной извести (содержание глины не более 8%), или гидравлической извести (содержание глины в породе не более 8 - 20%). Отличительной особенностью воздушной извести является то, что она твердеет только на воздухе и не обладает водостойкостью, а гидравлическая известь имеет более быстрое твердение и приобретает водостойкость - после ее твердения на воздухе не менее двух недель возможно ее помещение в водную среду. Наибольшее распространение имеет воздушная известь и при ее производстве под воздействием температуры происходит следующая химическая реакция СаСО 3 →СаО+СО 2
При этом карбонат кальция теряет с углекислым газом (СО 2) до 44% своей массы, становится легким и пористым. Получаемый в таком случае продукт - комовая негашеная известь (мелкопористые куски размером 5-10 см). В дальнейшем комовую негашеную известь подвергают либо гашению с использованием воды или дополнительному размолу с получением негашеной порошкообразной извести.
ГАШЕНАЯ ИЗВЕСТЬ |
В зависимости от количества воды используемой для гашения комовой извести возможно получение следующих продуктов:
- Гидратная известь ( пушонка)
- Известковое тесто
- Известковое молоко
Гидратная известь ( пушонка)
Тончайший белый порошок, полученный гашением извести, обычно в заводских условиях (гидраторы непрерывного действия) небольшим количеством воды (несколько выше теоретически необходимого - 50-70% воды от массы извести). При гашении в пушонку известь увеличивается в объеме в 2 - 2,5 раза.
Насыпная плотность - 400-450 кг/м 3
Влажность - не более 5%
Известковое тесто
Получается при гашении извести водой, когда количество воды в 3-4 раза превышает массу комовой извести. Процесс гашения производится в специальных гасильных ящиках (творилах). В ящик загружают комовую известь не более чем на 1/3 его высоты (толщина слоя примерно 10 см), поскольку при гашении известь увеличивается в объеме в 2,5-3,5 раза. Быстро гасящуюся известь заливают сразу большим количеством воды, чтобы не допустить перегрева и кипения воды, медленногасящуюся — небольшими порциями, следя за тем, чтобы известь не охладилась. Из 1кг комовой извести в зависимости от ее качества получают 2-2,5 литра известкового теста. Содержание воды в известковом тесте не нормируется. Обычно в хорошо выдержанном тесте соотношение воды и извести около 1:1. Время, необходимое для окончательного завершения процесса гашения, составляет не менее двух недель.
Известковое молоко
При гашении количество воды превышает теоретически необходимое в 8-10 раз.
НЕГАШЕНАЯ ПОРОШКООБРАЗНАЯ ИЗВЕСТЬ |
Преимущество порошкообразной извести негашеной перед комовой состоит в том, что при затворении водой она ведет себя подобно гипсовым вяжущим: сначала образует пластичное тесто, а через 20-40 мин схватывается. Это объясняется тем, что вода затворения, образующая тесто, частично расходуется на гашение извести. При этом известковое тесто густеет и теряет пластичность. Благодаря меньшему количеству свободной воды материалы на основе порошкообразной извести менее пористые и более прочные. Кроме того, известь при гашении разогревается, что облегчает работу с ней в холодное время. В зависимости от качества извести, необходимая для затворения вода составляет 100-150% от массы извести (определяется опытным путем).
Наиболее важнейшими показателями качества негашеной порошкообразной извести является:
- Активность - процентное содержание окислов, способных гаситься.
- Количество непогасившихся зерен (недожог или пережог).
Недожог (неразложившийся САСО 3), получающийся при слишком низкой температуре обжига, снижает качество извести, т.к. не обладает вяжущими свойствами.
Пережог образуется при слишком высокой температуре обжига. Зерна пережога медленно гасятся и могут вызвать растрескивание и разрушение уже затвердевшего материала.
- Время гашения. В зависимости от времени гашения известь подразделяется на виды:
- быстрогасящаяся - до 8 мин
- среднегасящаяся - до 25 мин
- медленногасящаяся - не менее 25 мин
По характеристикам состава известь подразделяется на 3 сорта
Наименование показателя |
Сорт |
||
1 |
2 |
3 |
|
не менее, % |
90 |
80 |
70 |
11 |
14 |
ОБЛАСТЬ ПРИМЕНЕНИЯ ИЗВЕСТИ |
Строительство Известь используется для приготовления строительных растворов, в производстве известково-пуццолановых вяжущих, в производстве термоизоляционных материалов, для изготовления искусственных каменных материалов - силикатного кирпича, газосиликатных блоков, а также в производстве покрасочных составов, в производстве сухих строительных смесей: штукатурных, клеевых, затирок швов, кладочных составов, шпатлевок. |
|
Водоочистка и водоподготовка Известь смягчает воду, осаждает органические вещества, находящиеся в воде, а также производит нейтрализацию кислых природных и отбросных сточных вод. |
|
|
Сельское хозяйство При внесении извести в почву устраняется вредная для сельскохозяйственных растений кислотность. Почва обогащается кальцием, улучшается обрабатываемость земли, ускоряется гниение гумуса, при этом заметно снижается потребность во внесении больших доз азотных удобрений. В животноводстве и птицеводстве гидратная известь используется для подкормки с целью устранения дефицита кальция в рационе животных, а также для общего улучшения санитарных условий содержания скота. |
|
Техника безопасности при работе с известью Воздушная известь всех видов - довольно сильная щелочь. Поэтому при работе с ней необходимо принимать меры, предотвращающие контакт извести с открытыми участками кожи и особенно дыхательных путей и глаз. Особенно опасна негашеная известь. Концентрация известковой пыли в воздухе не должна превышать 2 мг/м 3 . |
ООО « ГеоСтиль» +7 495 663 93 93 предлагает гашеную гидратную известь Сорт извести
84,39
68,04
67,32
71,0
5,80
2,98
1,0
2,7
Влажность, %
0,87
0,36
0,5
0,28
Тонкость помола:
Остаток частиц на сите с сеткой № 02, %
0,19
1,48
0,0
0,0
Остаток частиц на сите с сеткой № 008, %
1,28
9,20
1,0
0,31
ООО « ГеоСтиль» предлагает для своих клиентов
высококачественную молотую негашеную кальциевую известь 2-го сорта без добавок
производства ОАО « Завод производства извести» (Владимирская обл.)
Показатели качества молотой негашеной извести
ГОСТ 9179-77
ОАО « Завод производства извести»
Наименование показателя |
Результат анализа |
Сорт |
второй |
80,10 |
|
в т.ч. МgO, % |
2,34 |
Скорость гашения, мин. |
|
Гидратная вода, % |
1,5 |
Температура гашения, о С |
90 |
Дисперсность: |
|
Остатки на сите № 02, % |
1,5 |
Остатки на сите № 008, % |
15 |
Cтраница 1
Известковое молоко, приготовляемое непосредственно на заводе после дробления и гашения извести в специальных гасильных барабанах, добавляют в динасовую массу для придания сырцу необходимой механической прочности в процессе его сушки и обжига из расчета 2 5 % СаО в пересчете на сухую смесь.
Известковое молоко должно иметь удельный вес 1 045 - 1 060, что соответствует содержанию извести СаО 56 - 75 г в 1 л известкового молока.
Известковое молоко поступает в резервуар концентрированного молока и перекачивается насосами 2НП в расходные резервуары, где насосами типа НФ поддерживается во взвешенном состоянии. Эти же насосы подают известковое молоко на дозирование.
Известковое молоко, полученное в генераторе при разложении карбида, поступает в отстойник 5 непрерывного действия со скребковой мешалкой, которая перемещает отстоявшийся ил к центральному спускному штуцеру. Известковый ил перекачивается затем специальным насосом в отстойные ямы. Осветленный раствор гидроокиси кальция в воде из отстойника 5 через холодильник 4 возвращается в напорный бак 3, где к нему добавляется некоторое количество свежей воды для компенсации ее потерь.
Известковое молоко (10 % - ный раствор) приготавливают из гашеной извести в специальных резервуарах, оборудованных механическими мешалками. Для непрерывной работы отделения, в котором осуществляют очистку сточных вод, необходима установка по крайней мере двух резервуаров с известковым молоком, работающих по очереди. Известковое молоко подается в необходимом количестве в камеру реакции, через которую протекают сточные воды, подвергаемые нейтрализации. С целью обеспечения хорошего перемешивания известкового молока со сточными водами следует применять механические мешалки, работающие со скоростью 30 - 40 об / мин.
Работа сделанна в 2008 году
Приготовление известкового молока - Доклад, раздел Химия, - 2008 год - Производство кальцинированной соды Приготовление Известкового Молока. Известковое Молоко, Необходимое В Содовом...
Приготовление известкового молока. Известковое молоко, необходимое в содовом производстве для регенерации аммиака из хлористого аммония по реакции 2NH4C1 Са ОН 2 CaCl2 2NН3 2Н2О, получают гашением извести избытком воды СаО Н2О Са ОН 2 В воде Са ОН 2 растворяется плохо, причем с повышением температуры растворимость уменьшается.
При 0 С растворяется 0,185 г на 100 г Н2О, а при 100 С всего лишь 0,077 г па 100 г Н2О. Поэтому для разложения хлористого аммония применяют не гомогенный раствор, а суспензию Са ОН 2 в воде, называемую известковым молоком. Концентрация взвешенной гидроокиси кальция в известковом молоке должна быть по возможности высокой, так как чем меньше воды поступит с известковым молоком в отделение дистилляции, где регенерируется аммиак, тем меньше тепла пара будет израсходовано на нагревание этой воды в процессе регенерации.
Максимально возможная концентрация известкового молока ограничивается его вязкостью слишком вязкую суспензию трудно транспортировать, очищать от примесей и дозировать. Вязкость суспензии зависит не только от концентрации взвешенной Са ОН 2, но и от температуры. С повышением температуры вязкость уменьшается. Поэтому известковое молоко получают при высокой 90 С температуре, которая обеспечивается применением для гашения горячей воды, а также выделением тепла в процессе самой реакции гашения.
Это тепло могло бы повысить температуру известкового молока примерно на 75 С, но практически значительная часть тепла теряется в процессе гашения на испарение воды и теплоизлучение. Поэтому известковое молоко с температурой 90-95 С можно получить, используя для гашения воду, подогретую до 60-65 С. На качество известкового молока заметно влияет качество извести. Имеет, например, значение температура, при которой обжигалось карбонатное сырье чем она выше, тем медленнее гасится полученная известь и тем менее дисперсным получается известковое молоко.
При слишком высокой температуре обжига выше 1350 С получается известь, которая практически уже не гасится водой. Из примесей, встречающихся в извести, больше всего влияет па продолжительность гашения сульфат кальция. Высокая степень дисперсности известкового молока имеет значение не только для скорости разложения хлористого аммония.
Высокодиспергированная суспензия труднее расслаивается, лучше сохраняет свою однородность, что важно при дозировке, не засоряет трубопроводы и меньше изнашивает насосы и коммуникации. Примерный состав известкового молока следующий Са ОН 2 . 200 - 250 н.д. Mg OH 2 1 - 2 г л СО2-3 7 - 14 н.д. СаSO4 1 - 3 г л SiO2 нерастворимые в воде HCl примеси 10 - 20 г л R2O3 5 - 8 г л Плотность.1,26 Технологическая схема получения известкового молока Технологическая схема получения известкового молока включает две основные операции гашение извести горячей водой и очистку известкового молока от крупных кусков и мелких зерен недопала, перекала и других нерастворимых примесей.
Движение материальных потоков но отдельным аппаратам показано на рис. 8. Из рабочего бункера 2 известь подастся лотковым питателем 1 во вращающийся барабан-гаситель 3, куда одновременно поступают нагретая вода и промывные воды после промывки отбросных примесей извести слабое известковое молоко. 8 Рис. 8 технологическая схема приготовления известкового молока 1 - лотковый питатель 2 - рабочий бункер 3 - барабан - гаситель 4 - конденсатор 5 - сортировочный барабан для крупного недопала 6 - транспортер 7 - сортировочный барабан 8 - шнек 9 - шаровая мельница мокрого помола 10 - мешалка неочищенного слабого известкового молока 11 - виброгрохот 12 - мешалка очищенного слабого известкового молока 13 - мешалка отбросного шлама 14 - классификатор 15 - мешалка концентрированного известкового молока. В гасителе 3 известь гасится и образуется известковое молоко с примесью различного размера кусков недопала, перекала и прочих непогасившихся частиц извести.
Известковое молоко вместе с примесями поступает из гасителя 3 в сортировочный барабан 5 для крупною недопала, представляющий собой сито с отверстиями размером 40 мм. Сортировочный барабан для крупного недопала является продолжением гасителя, вращается вместе с ним и служит для отделении от известкового молока крупных кусков недопала. Известковое молоко, проходя через отверстия в барабане, поступает для дальнейшей очистки в сортировочный барабан 7 для мелкого недопала.
Крупные куски недопала размером более 40 мм в конце барабана промываются горячей водой, поступают на транспортер 6 и передаются в известковые печи для повторного обжига.
Сортировочный барабан 5 для крупного недопала заключен в кожух, оборудованный двумя вытяжными трубами для удаления образующегося в гасителе пара. Одна труба идет к конденсатору 4, где пар из гасителя, конденсируясь, подогревает воду, идущую на гашение, а вторая труба отведена в атмосферу на случай ремонта или чистки конденсатора, В сортировочном барабане 7 для мелкого недопала, представляющем собой вращающееся перфорированное сито с отверстиями 2Ч10 мм, от известкового молока отделяются частицы, имеющие размер более 2 мм. Известковое молоко, проходя через сито, попадает в конусообразный приемник кожуха, в который заключен сортировочный барабан, откуда идет для окончательной очистки от примесей в классификатор 14. Оседающий на дно классификатора шлам выгребается реечным механизмом, промывается горячей водой и поступает в мешалку шлама 13. Концентрированное молоко, освобожденное от шлама, подается в мешалку известкового молока 15 л далее по своему назначению - в отделение дистилляции.
Оставшиеся в сортировочном барабане твердые частицы размером более 2 мм при вращении барабана постепенно перемещаются вдоль него и выгружаются в шнек 8, при помощи которого подаются в шаровую мельницу мокрого помола 9. В мельнице одновременно с размолом происходит гашение извести, вскрываемой при размоле кусочков перекала.
Получающееся в мельнице слабое известковое молоко вместе с примесями перетекает в мешалку 10, куда отводится также слабое известковое молоко, образующееся при промывке недопала.
Для очистки от шлама слабое известковое молоко из мешалки 10 откачивают центробежным насосом в виброгрохот 11. Шлам из виброгрохота поступает в мешалку отбросного шлама 13, а очищенное слабое известковое молоко попадает в мешалку очищенного слабого молока 12, откуда насос подает его в гаситель.
Шлам из классификатора 14 и виброгрохота 11 разбавляется в мешалке 13 отбросной жидкостью дистиллера и центробежным насосом откачивается в накопитель отбросной жидкости - так называемое белое море. Нормы технологического режима отделения известкового молока, их регулирование и контроль Наиболее важные регламентируемые показатели, характеризующие качество известкового молока и обеспечивающие нормальную работу отделения дистилляции, это концентрация Са ОН 2 или свободного СаО и температура молока.
На содовых заводах концентрацию свободного СаО в известковом молоке называют титром молока, так как ее определяют обычным титрованием молока соляной кислотой. Для производства необходимо, чтобы содержание Са ОН 2 в известковом молоке было возможно выше, так как при этом уменьшается объем дистиллерной жидкости, а следовательно, повышается производительность отделения дистилляции и уменьшаются расход пара и потери извести и аммиака с отбросной жидкостью дистиллера.
Однако чрезмерно высокая концентрация Са ОН 2, повышая вязкость суспензии, создает затруднения в работе гасителя и очистке молока от примесей. Практика показала, что допустимая концентрация Са ОН 2 в молоке титр может быть в пределах 200-250 н. д. Кроме того, колебания титра молока должны быть минимальными, так как они усложняют регулирование дозировки молока в отделении дистилляции и повышают потери извести и аммиака с отбросной жидкостью дистиллера.
В отбросной жидкости допускаются колебания свободного СаО 1-2 н. д т.е. в пределах одного нормального деления. В аппаратах отделения дистилляции известковое молоко разбавляется примерно в 4 раза. Отсюда следует, что колебания титра молока не должны превышать 4 н. д. Титр молока регулируют путем изменения количества воды, подаваемой на гашение. Колебания титра выравнивают в сравнительно больших емкостях - мешалках известкового молока.
Количество извести, подаваемой в гаситель, определяется расходом известкового молока потребляющими цехами кальцинированная сода, каустик, водоочистка и пр О концентрации Са ОН 2 в известковом молоке в первом приближении можно судить по его плотности, измерить которую легко может аппаратчик непосредственно в цехе. Для более точного определения каждые 30 мин. производят анализ на содержание свободного СаО в цеховой лаборатории. Возможность получения известкового молока с высоким титром свободного СаО ограничена вязкостью получаемого молока, которая зависит не только от концентрации, но и от температуры. С повышением температуры вязкость молока уменьшается, улучшаются условия для его очистки от примесей, а также облегчаются его транспортирование и дозировка.
Поэтому для получения молока с высоким титром необходимо проводить гашение извести при повышенной температуре. Нормы технологического режима предусматривают конечную температуру молока 85-95 С. Эта температура в значительной мере зависит от температуры, поступающей на гашение воды, подогреваемой за счет тепла конденсации водяных паров, выходящих из гасителя.
Для подогревания можно использовать отработавшую воду из холодильника газа содовых печей или из холодильника газа дистилляции. В нормах технологического режима предусмотрено содержание СО32- в известковом молоке в количестве 7-12 н. д. Эта величина характеризует содержание в молоке CaCO3, бесполезной неактивной извести, которая практически не вступает во взаимодействие с NH4C1, т. е. степень очистки молока от примесей.
Очищать известковое молоко надо до экономически разумных пределов, так как с повышением степени очистки процесс усложняется. Норма содержания СО32- в известковом молоке и указывает этот разумный предел. Абсорбция Назначение абсорбера состоит в том, чтобы произвести окончательное насыщение рассола из промывателя колонн аммиаком. Рассол поваренной соли, содержащий 310 г л хлорида натрия, предварительно очищенный от примесей других солей, поступает в абсорбер, в который подают аммиак из колонны дистилляции, где протекает регенерация аммиака и маточной жидкости после вакуум - фильтров.
Также в абсорбер поступает газ, содержащий аммиак и углекислоту из печи кальцинации бикарбоната. При плохой очистке рассола от солей кальция и магния в процессе аммонизации могут происходить побочные нежелательные реакции аммиак и углекислота будут взаимодействовать с солями кальция и магния, образуя осадки углекислого кальция и гидроокиси магния, которые могут отлагаться на стенках аппаратов и трубопроводов.
При систематическом нарушении режима очистки рассола отложения CaCO3 и Mg OH 2 на стенках аппаратов и трубопроводов могут нарушить нормальную работу отделения абсорбции. Весь процесс абсорбции зависит, главным образом, от двух факторов 1 от количества газов, приходящих в абсорбер из колонны дистилляции и печи кальцинации бикарбоната 2 от количества рассола, поступающего на дистилляцию, то регулирование процесса абсорбции заключается в регулировании поступления рассола в таком количестве, чтобы насыщенная аммиаком жидкость имела необходимую концентрацию.
Технологическая схема отделения абсорбции Технологическая схема отделения абсорбции должна обеспечить высокую степень очистки выхлопных газов от аммиака, для чего необходимо промывать эти газы свежим рассолом, содержащим минимальное количество аммиака. Абсорбция диоксида углерода идет значительно медленнее, чем аммиака, поэтому аппаратура должна быть рассчитана так, чтобы обеспечивать поглощение заданного количества аммиака и максимально возможного количества диоксида углерода.
Свежий рассол, прежде всего, используют для поглощения аммиака из выхлопных газов. Около 75-80 рассола поступает из напорного бака 3 в промыватель воздуха фильтров ПВФЛ 4, где поглощается аммиак из воздуха, проходящего через фильтрующую ткань вакуум-фильтров и содержащего примерно 0,5-1 NH3. После ПВФЛ рассол идет во второй промыватель газа колонн ПГКЛ-2 7, где поглощается аммиак из отходящих газов отделения карбонизации, содержащих до 10 NH3. Остальные 20-25 свежего очищенного рассола из напорного бака 3 поступают в промыватель газа абсорбции ПГАБ 1, где поглощается аммиак из отходящих газов отделения абсорбции, содержащих до 5 NH3. Попутно поглощается некоторое количество углекислоты, содержащейся в выхлопных газах. Газ из ПВФЛ поступает на вакуум-насос 5, создающий разрежение на вакуум-фильтрах, и выбрасывается в атмосфер.
Газ из ПГАБ также поступает на вакуум-насос 2. Он содержит не менее 75 СО2, поэтому вакуум-насос передает его на смешение с углекислым газом содовых печей и затем на-карбонизацию.
Выхлопные газы из ПГКЛ-2выбрасывают в атмосферу. Рис.8. Типовая технологическая схема отделения абсорбции 1-промыватель газа абсорбции 2,5-вакуум-насосы 3-напорный бак 4-промыватель воздуха фильтров 6-холодильник газа дистилляции 7-второй промыватель газа колонн 8-сепаратор-брызгоуловитель 9 - сборник амминизированного рассола 1 0, 12-оросительные холодильники 11-постамент резервуар 13-второй абсорбер 14-первый абсорбер Рассол после промывки выхлопных газов из ПГКЛ-2 и ПГАБ поступает на основную операцию - поглощение аммиака из газа дистилляции, осуществ-ляемое в две ступени - в первом абсорбере АБ-1 14 и во втором абсорбере АБ-2 13. Две ступени абсорбции вызываются необходимостью в промежуточном охлаждении рассола, нагревающегося от растворения и взаимодействия NH3 и СО2 и от конденсации водяного пара, поступающего с газом дистилляции, После первого абсорбера рассол, нагретый до температуры 60- 65 С, охлаждают до 28-32 С в оросительном холодильнике 12, после чего он поступает во второй абсорбер, где также нагревается примерно до 65 С и поэтому прежде, чем поступить в сборник аммонизированного рассола САР 9, вторично охлаждается в оросительном холодильнике 10. Чтобы обеспечить самотек рассола на оросительный холодильник, второй абсорбер и стоящие на нем аппараты расположены на постаменте - резервуаре 11. Газ из отделения дистилляции сначала охлаждается и осушается в холодильнике газа дистилляции ХГДС 6 охлаждающей водой и затем, пройдя сепаратор - брызгоуловитель 8, противотоком к рассолу проходит последовательно второй и первый абсорберы, где аммиак поглощается почти целиком.
Вместе с аммиаком из газа поглощается большая часть углекислоты.
Непоглотившиеся газы идут в ПГАБ 1 . При охлаждении газа дистилляции в ХГДС водяные пары конденсируются, образуя конденсат, содержащий до 150-200 н. д. аммиака и углекислоту.
Аммиак из таких жидкостей, называемых слабыми, регенерируют на отдельной установке.
Получаемый при этом газ, содержащий NН3, CO2 и Н2О и охлажденный до 58-60 С, поступает обычно в первый абсорбер. Карбонизация аммонизированного рассола Процесс карбонизации насыщения аммонизированного рассола диоксидом углерода, в результате которого образуется гидрокарбонат натрия, является основным процессом содового производства.
В отделении карбонизации получают заданное количество содержащей гидрокарбонат натрия суспензии в виде непрерывного материального потока, передаваемого в отделение. Качество суспензии определяется качеством содержащегося в ней продукта- гидрокарбоната натрия. Очень часто о качестве гидрокарбоната натрия судят по его фракционному составу. Определяющей оценкой качества суспензии является содержание остаточной влаги в гидрокарбонате натрия, полученном фильтрацией этой суспензии в стандартных условиях.
Оценку работы карбонизационной колонны можно дать, используя безразмерный технический критерий оптимальности И хс хссвяз 4.2-0.lщс хс -расход суспензии, выходящей из карбонизационной колонны, м3 с хссвяз - концентрация связанного аммиака в осветленной части суспензии, н.д. щс - содержание остаточной влаги в гидрокарбонате натрия Чем выше производительность по гидрокарбонатy натрия и меньше остаточная влага в продукте, тем лучше работает карбонизационная колонна, т. е. необходимо стремиться к увеличению абсолютного значения критерия оптимальности.
В результате процесса карбонизации из раствора в осадок выпадает гидрокарбонат натрия, образующийся по реакции NaCl NH3 СО2 Н2О - NaHCO3 NH4C1. Эта реакция характеризует только конечный результат взаимодействия хлорида натрия и гидрокарбоната аммония. В действительности процесс карбонизации протекает гораздо сложнее, и его механизм до настоящего времени окончательно не выяснен.
Процесс карбонизации ведут ступенчато. Вначале аммонизированный рассол обрабатывают газом известковых печей в колонне предварительной карбонизации КЛИК, затем в первом промывателе газа колонн ПГКЛ-1 - газами, отходящими из осадительных колонн, и, наконец в осадительных колоннах КЛ,в нижнюю часть которых вводят смешанный газ 65-75 СО2 , а в среднюю часть -газ известково-обжигательных печей. На первой стадии карбонизации большая часть диоксида углерода связывается в карбамат аммония 2NH3 СО3 NH2COONH4, который затем гидролизуется NH2COONH4 Н2О - NH4HCO3 NH3, с образованием пересыщенного по НСОз- раствора.
Затем из пересыщенного раствора кристаллизуется гидрокарбонат натрия, образующийся по реакции NH4HCO3 NaCl - NaHCO3 NH4Cl. Процесс насыщения аммонизированного рассола диоксидом углерода является экзотермическим. Выделяющееся тепло реакции в конечной стадии процесса необходимо отвести, чтобы обеспечить необходимые степени карбонизации раствора и утилизации использования натрия. Температурный режим карбонизационной колонны значительно влияет на процесс образования кристаллов гидрокарбоната натрия.
Для получения крупных кристаллов гидрокарбоната натрия правильной формы, которые не забивают фильтрующую поверхность вакуум-фильтров и малорастворимы в процессе фильтрации, необходимо поддерживать сравнительно высокую температуру 60-72 С в зоне образования и в начальный период роста кристаллов. В процессе дальнейшего роста кристаллов температура уже не оказывает существенного влияния на их размер. Процесс кристаллизации начинается с образования зародышей в виде очень мелких кристалликов гидрокарбоната натрия, из которых при поддержании нормального технологического режима образуются кристаллы в форме коротких цилиндров - бочки. При ухудшении процесса кристаллизации образуются кристаллы, имеющие форму длинных цилиндров и склонные к образованию сростков в виде снопов друзы. В этом случае выделяется большое количество мелочи в виде игольчатых кристаллов и бесформенных обломков. Такие кристаллы при фильтрации уплотняются и удерживают в образовавшихся мелких ячейках много влаги, т. е. увеличивается содержание остаточной влаги в гидрокарбонате натрия.
Технологическая схема отделения карбонизации Аммонизированный рассол из сборника аммонизированного рассола САР поступает в колонну предварительной карбонизации КЛПК, в которую подается также газ известковых печей, содержащий 32-36 об. СО2 при обжиге мела и 38-40 об. СО2 при обжиге известняка.
Из КЛПК жидкость при температуре 42-46 С направляется в первый промыватель газа колонн ПГКЛ-1 . Сюда же поступает газ из КЛПК и осадительных колонн.
В ПГКЛ-1улавливается аммиак, отдутый карбонизующим газом из КЛПК. За время прохождения жидкости через ПГКЛ-1 ее температура повышается на 5-8 С. Для дополнительного охлаждения жидкости после ПГКЛ-1 предусматривается теплообменник, откуда жидкость поступает в осадительную карбонизационную колонну. В нижнюю часть колонны подается смешанный газ первый ввод, содержащий диоксид углерода 70-80 об а в среднюю часть - газ известковых печей второй ввод. Газ из осадителной карбонизационной колонны направляется в ПГКЛ-1, а суспензия-в отделение фильтрации.
Карбонизационные колонны работают сериями, чтобы обеспечить непрерывность потока суспензии, направляемого в отделение фильтрации. Наибольшее распространение получили серии, состоящие из четырех карбонизационных колонн, из которых три работают в качестве осадительных, а одна - колонна предварительной карбонизации.
Аппаратура отделения карбонизации Карбонизационная колонна КЛ. Она является основным аппаратом отделения карбонизации. КЛ представляет собой цилиндрическую пустотелую колонну диаметром до 3 и высотой до 27 м, состоящую из ряда чугунных бочек или царг. Сверху через штуцер 5 и колонну поступает из ПГКЛ-1 подлежащий карбонизации раствор, а снизу через штуцер 2 и в середине через штуцер 9- углекислый газ. При работе колонна заполнена раствором до определенного постоянного уровня. Рис.9. Карбонизационная колонна диаметром 2680 мм 1-бочка-база 2-штуцер для входа газа 3-холодильная бочка 4-абсорбционная бочка 5-штуцеры для входа жидкости 6-сепарационные бочкм 7-штуцеры для выхода газа 8-барботажная колонна 9-штуцер для входа газа 10-штуцер для выхода суспензии.
Осуществлению принципа противотока может препятствовать продольное перемешивание жидкости газом по высоте колонны. Чтобы это перемешивание свести к минимуму, между отдельными бочками 4 колонны устанавливают пассеты, или барботажные тарелки 8.Тарелка состоит из днища 2 и перекрывающего его колпака 1. Барботажные тарелки препятствуют продольному перемешиванию жидкости в колоне и обеспечивают равномерное распределение газа по сечению колонны и способствуют увеличению поверхности контакта между газом и жидкостью.
В верхней части колонны установлены две пустые сепарационные бочки 6, предназначенные для отделения увлекаемых газом брызг жидкости и имеющие водомерные стекла для наблюдения за уровнем жидкости в колонне. Сверху колонна закрыта крышкой, на которой находится штуцер 7 для выхода газа и для установки предохранительного клапана.
В основе карбонизационной колонны установлена бочка-база 1 со сферическим днищем и штуцерами 10 и 2, через которые выводится суспензия бикарбоната натрия и подается компрессором смешанный газ 1-го ввода. Бочки и барботажные тарелки колонны изготавливают из чугуна. Тонкостенные трубки в холодильных бочках толщиной 6мм делают из углеродистой стали или из специального чугуна, содержащего 0,5 Ni,0,4 Mn,3,3 C и 0,4 Cr.
Конец работы -
Эта тема принадлежит разделу:
Производство кальцинированной соды
Добывалась она до конца восемнадцатого века преимущественно из естественных месторождений Венгрии, Египта и других частей Африки и из золы морских… Сода того времени не отличалась чистотой. В 1775 г. французская академия… Метод Леблана Способ Леблана состоял в приготовлении из поваренной соли при помощи серной кислоты сульфата и…
Если Вам нужно дополнительный материал на эту тему, или Вы не нашли то, что искали, рекомендуем воспользоваться поиском по нашей базе работ:
Что будем делать с полученным материалом:
Если этот материал оказался полезным ля Вас, Вы можете сохранить его на свою страничку в социальных сетях:
17
ФЕДЕРАЛЬНОЕ АГЕНТСТВО ПО ОБРАЗОВАНИЮ
ПЕРМСКИЙ ГОСУДАРСТВЕННЫЙ ТЕХНИЧЕСКИЙ УНИВЕРСИТЕТ
БЕРЕЗНИКОВСКИЙ ФИЛИАЛ
КАФЕДРА ТЕХНОЛОГИИ И МЕХАНИЗАЦИИ ПРОИЗВОДСТВ
КУРСОВОЙ ПРОЕКТ
ПО КУРСУ: « ТЕХНОЛОГИЧЕСКИЕ ПРОЦЕССЫ И ПРОИЗВОДСТВА»
ТЕМА: «Расчет аппарата гашения извести в производстве известкового м о лока на ОАО «АВИСМА »
Выполнил: ст. гр. АТП-01(в) Гаврюшин К.Г.
Проверил: ст. преподаватель Демин Д.Ю.
Березники 2005 г.
стр. |
|
ВВЕДЕНИЕ |
|
МАТЕРИАЛЬНЫЙ БАЛАНС КАМЕРЫ ПРЕДВАРИТЕЛЬНОГО ОХЛАЖД Е НИЯ |
|
ТЕПЛОВОЙ БАЛАНС КАМЕРЫ ПРЕДВАРИТЕЛЬНОГО ОХЛАЖДЕНИЯ |
|
ТЕХНОЛОГИЧЕСКИЙ РАСЧЕТ КАМЕРЫ ПРЕДВАРИТЕЛЬНОГО ОХЛАЖД Е НИЯ |
11 |
ЗАКЛЮЧЕНИЕ |
12 |
СПИСОК ЛИТЕРАТУРЫ |
13 |
ВВЕДЕНИЕ
Гашеную известь получают действием определенного количества воды на нег а шеную известь, в результате которого образуется в виде порошка (пушенки), извес т кового теста или известкового молока.
Известковое молоко образуется при введении количества воды, пр е вышающего теоретически необходимое более чем в десять раз. Средний размер частиц при гаш е нии в известковое молоко равен одному микрону. При дальнейшем увеличении кол и чества воды продукт гашения н о сит название известковой воды.
Основные требования к качеству известкового молока.
Гидроксид кальция представляет собой суспензию, полученную при взаимодейс т вии оксида кальция с водой.
Плотность Са(ОН) 2 в зависимости от концентрации и массы прим е сей колеблется в пределах 1,15 1,30 г/см 3 , удельный вес 1,2 г/см 3 . В воде Са(ОН) 2 растворяется плохо, причем с повышением температуры растворимость уменьшается. Максимально возможная концентрация известкового молока ограничивается его вязкостью. Вя з кость суспензии зависит не только от концентрации взвешенного Са(ОН) 2 , но и от температуры. Поэтому известковое молоко получают при высоких темпер а турах (90 0 С).
Суспензия Са(ОН) 2 является сильной щелочью, относится ко второму классу опасн о сти. Действует на кожу прожигающе, растворяя белки. При вдыхании аэрозолей выз ы вает изменения слизистых оболочек верхних дыхательных путей, наблюдаются хрон и ческие бронхиты. Пр е дельно - допустимая концентрация в виде аэрозоля 0,5 мг/м 3 . Опасно попадания в глаза, так как приводит к потере зрения. Эти опасные свойства возрастают с повышением температуры молока. Работающие с известковым молоком должны иметь спецодежду: резиновые сапоги, брезентовые костюмы, защитные очки, каски и рукавицы.
Гидроксид кальция, на ОАО «АВИСМА», применяется для очистки от вредных веществ отходящих газов и промышленных стоков.
ОПИСАНИЕ ТЕХНОЛОГИЧЕСКОЙ СХЕМЫ ПРОИЗВОДСТВА
Гашение извести протекает по реакции:
CaO + H 2 O = Ca (OH ) 2 + 15,93 ккал.
Изменяя количество воды, подаваемой на гашение, можно пол у чить известь порошок (тонкий порошок), известковое тесто (густая н е текучая масса), известковое молоко водную суспензию Ca (OH ) 2 .
Гидратация оксида кальция является обратимой реакцией, напра в ление которой зависит от температуры и давления водяных паров в о к ружающей среде. Упругость диссоциации Ca (OH ) 2 на CaO и H 2 O достигает атмосферного давления при температ у ре 547 0 С, одн а ко гидрат окиси Са может частично разлагаться и при более низкой температуре. Для того чтобы процесс шел в нужном направлении, необходимо стр е миться к повышению упругости водяных паров над Ca (OH ) 2 и не допу с кать слишком высокой температуры. Вместе с тем следует избегать и переохлаждения гасящейся и з вести, так как оно может значительно з а медлить процесс гашения извести. На процесс гашения значительно влияют температура воды и реагирующей смеси. Реакция обр а зования Ca (OH ) 2 экзотермическая, избыточная влага нагревается за счет выд е ленного тепла.
С ростом температуры выделившийся гидрат окиси кальция вып а дает в осадок и обволакивает поверхность кусков негашеной извести. В результате прекращается с о прикосновение негашеной извести с водой и процесс гашения прекращается.
Температура воды при прекращении гашения понижается, раств о римость Ca (OH ) 2 увеличивается, пленка Ca (OH ) 2 на кусках негашеной извести вновь раствор я ется и процесс гашения возобновляется. Следовательно, процесс гашения извести с о провождается явлением «самото р можения». Поэтому лучше результаты получаются при ведении пр о цесса гашения в среде с постоянной температурой.
Активность извести зависит от размера кристаллов CaO и степени нарушения кристаллической решетки. По мере повышения температуры обжига размеры криста л лов увеличиваются, степень нарушения кристаллической решетки уменьшается, и а к тивность гашеной извести сн и жается.
Продукты взаимодействия извести с окислами кремния, алюминия, железа (с и ликаты, алюминаты, ферриты) понижают способности изве с ти к гидратации.
При гашении эти примеси присоединяют к себе одну или несколько молекул воды, образуя гидросиликаты, гидроалюминаты кальция, которые не переходят в извес т ковое молоко. Процесс гидратации в этом случае сопровождается набуханием и переходом этих соединений в студн е образное состояние.
Обожженная известь, если она долго лежит на воздухе, обнаруж и вает явление «пассивности». При долгом нахождении на воздухе начинается самопроизвольное г а шение за счет влаги воздуха. Оболочка растворимой Ca (OH ) 2 , находящаяся на кусо ч ках извести, переходит в нера с творимую CaCO 3 , которая изолирует CaO от действия влаги.
2. Описание технологического процесса по операциям
Негашеная комовая известь из отделения обжига известняка транспортируется в отделение приготовления известкового молока (ОПМ) по поточно-транспортной схеме (ПТС).
Известь после дробления в щековой дробилке СМ-11Б поступает на реверси в ный транспортер, затем по транспортерам длиной 85810 мм и 19000 мм направляется в три расходных бункера (суммарной емк о стью 60 т).
Из расходных бункеров питателями ПКЛ-8-0 известь транспортируется в загр у зочные течки аппарата гашения извести АИ-1, 8М2. О д новременно в аппарат- гаситель подается горячая вода из бака подогр е ва с температурой не менее 60 0 с. Водяные пары, образующиеся при гашении извести, удаляются из аппарата- гасителя с помощью а с пирацио н но-технической установки.
Для удаления непрогасившихся кусков извести недопала выгр у зочная часть снабжена специальным устройством в виде спирали. Н е допал удаляется из гасителя на транспортер, затем на решетку, где происходит его классификация. Куски недопала, размером в поперечнике более 70 мм, с решетки по ленточному транспортеру напра в ляются в бункер- накопитель крупного недопала. Куски недопала, размером в поп е речнике менее 70 мм, проваливаются через решетку в бункер- накопитель мелкого н е допала и вывозится автотранспортом.
Полученное известковое молоко из аппарата гашения извести стекает в спец и альный классификатор.
Очистка известкового молока в классификаторе происходит за счет разности удельных весов, крупности С a (OH ) 2 и наличия прим е сей.
Корпус классификатора представляет собой сварное полуцилиндрической фо р мы наклонное корыто. Для разгрузки песка в верхней ча с ти корыта имеется люк.
Спираль является транспортирующим механизмом и служит для перемешивания крупного класса песков из зоны осаждения до разгр у зочного люка. Твердая фракция при помощи шнека удаляется на тран с портер, а затем в бункер- накопитель песка. Нижняя часть апп а рата классифицирующий бассейн, в наклонной части которого от зе р кала осаждения до разгрузочного люка происходит обезвоживание песков.
После классификатора готовое известковое молоко поступает в приемные м е шалки (промежуточные баки) емкостью 16 м 3 , из которых центробежным насосом п е рекачивается две пары гидроциклонов в расходные мешалки (баки сборники). В ги д роциклонах происходит более тонкая очистка известкового молока. Очищенное мол о ко из гидроц и клонов через коллектор направляется в баки- мешалки емкостью 400 м 3 (4 штуки).
Примеси (пески) с нижней части гидроциклонов удаляются в кла с сификаторы, где происходит улавливание песков, которые направляю т ся по транспортеру в бункер- накопитель песка, а очищенное молоко из ги д роциклонов поступает в промежуточные баки.
В процессе получения известкового молока используется оборотная вода, кот о рая поступает из трубопровода комбината. Подогрев воды для гашения извести осущ е ствляется в аппарате погружного гор е ния (АПГ).
Полученное в баках сборниках товарное известковое молоко ко н центрацией не менее 100 г/дм 3 центробежным насосом непреры в но транспортируется в кольцевой трубопровод. Из кольцевого трубопровода через индивидуальные отводы осуществл я ется прием и з весткового молока в циркуляционные баки газоочисток.
Аппарат известегасительный представляет собой цилиндрический барабан, вр а щающийся на роликах со скоростью не более 4 об/мин., у с тановленный с уклоном 0,5 0 к выходу известкового молока. В центре за д ней крышки барабана имеется отверстие, куда вставляется течка для подачи в аппарат г о рячей воды, с температурой (6010) 0 С, и извести. Внутренняя часть барабана по всей длине имеет направляющие пласт и ны, установленные винтообразно под углом 12 0 к цилиндрообразующей барабана, бл а годаря чему известь, поступающая в загрузочную часть, постоянно соприкасаясь с горячей водой образует известковое молоко концентрацией не менее 100 г/дм 3 , пер е мещается вдоль оси барабана к выгрузо ч ной части.
МАТЕРИАЛЬНЫЙ БАЛАНС АППАРАТА ГАШЕНИЯ ИЗВЕСТИ
1.Исходные данные
1.1 Основная реакция
CaO + H 2 O = Ca (OH ) 2 + Q (65.4 кДж)
1.2 Характеристика исходных веществ и продуктов реакции
Таблица 1
CaO |
H 2 O |
Ca(OH) 2 |
|
Молекулярная масса, кг/кмоль Плотность, кг/дм 3 Пористость, % |
56 3,36 34-46 |
18 1,0 |
74 2,24 |
Отношение вода:известь-3,54
Комковатость извести 60:80 мм
Состав извести:
CaO 86%
CaCO 3 14% (В общее количество CaCO 3 включены также примеси содерж а щиеся в извести)
Температура поступающей извести: t 1 =50 0 С
Температура поступающей воды: t 2 =60 0 С
Температура выходящего известкового молока: t 3 =90 0 С
Производительность гасителя по извести: 120 т в сутки
Плотность раствора известкового молока: 1,2 кг/м 3
Потери извести с отбросами: недопал 7% веса
Потери известкового молока в недопале (на сухое вещество): 40% веса.
2. Материальный расчет
Расчет ведется на 1000 кг извести.
Часовая производительность гасителя (по извести)
G 1 = = = 5000 кг/ч
где G r производительность гас и теля по извести, кг
24 количество часов в сутках, ч
Количество CaO в исходном сырье:
G CaO = G 1 * 0,86 = 5000 * 0,86 = 4300 кг
где G 1 часовая производительность гасителя, кг/ч
0,86 содержание CaO в извести (в %)
На гашение такого количества извести требуется воды:
G 2 = кг
где G CaO - количество CaO в исходном сырье, кг
М CaO молярная масса CaO , кг/моль
M H 2 O молярная масса воды, кг/моль
При этом образуется такое количество Ca (OH ) 2
G Ca (OH )2 ===1826,2 кг
где G 2
M Ca (OH )2
М CaO молярная масса CaO , кг/моль
Количество воды подающейся на гашение
G 2 = G CaO * 3.5 = 4300 * 3.5 = 15050 кг
где G CaO - количество CaO в исходном сырье, кг
Количество воды в растворе известкового молока после гашения:
G H 2 O = G H 2 O - G 2 - G Ca (OH )2 = 15050 1382 1826,2 = 11841,8 кг
где G Н2О - количество воды в исходном сырье, кг
G 2 - количество воды подающейся на гашение, кг
G Ca (OH )2 количество известкового молока, кг
Потери CaO с недопалом:
G п = G CaO * 0,07 = 4300 * 0,07 = 301 кг
где G CaO - количество CaO в исходном сырье, кг
0,07 потери извести (от веса), в %
В гидратированном состоянии это будет соответствовать следу ю щему количеству Ca (OH ) 2 :
G отбр. Ca (OH )2 ===397,8 кг
где G п - потери CaO , кг
M Ca (OH )2 молярная масса известкового молока, кг/моль
М CaO молярная масса CaO , кг/моль
Что составляет 40 %, следовательно масса недопала:
G отбр . ===994,4 кг
При гашении испаряется некоторое количество воды, обозначим его Х .
Тогда к моменту отделения отбросов в растворе имелось воды:
G H 2 O =(11841,8 Х ) кг
С недопалом удаляется воды:
G H 2 O = (11841,8 - Х )*0,07=(828,9 - 0,07 Х ) кг
Состав суспензии выходящей из гасителя:
Ca (OH ) 2 : G Ca (OH )2 = 1826,2 397,8 = 1428,4 кг
H 2 O : G H 2 O = (11841,8 Х ) (828,9 0,07 Х ) = (11012,9 0,93 Х ) кг
Всего: (12441,3 0,93 Х ) кг
Х можно определить с помощью теплового баланса: Х =122,3 кг
Сводный материальный баланс гасителя.
Таблица 2
Компоне н ты |
Приход |
Расход |
||||
статьи прих о да |
всего |
статьи расх о да |
на р е акцию |
пот е ри |
всего |
|
CaO |
4300 |
4300 |
4300 |
4300 |
||
H 2 O |
15050 |
15050 |
1382 |
10899 |
942,64 |
13223,64 |
Ca(OH) 2 |
1428,4 |
397,8 |
1826,2 |
|||
Всего |
19350 |
19350 |
ТЕПЛОВОЙ БАЛАНС АППАРАТА ГАШЕНИЯ ИЗВЕСТИ
1. Приход тепла
1.1. С известью:
КДж,
где кДж / кг*град теплоемкость СаО.
1.2. От экзотермической реакции:
Q р = 65,4 кДж/моль СаО
кДж.
1.3. С водой:
КДж.
1.4. Теплота растворения:
кДж,
где кДж /моль теплота растворения Ca(OH) 2 .
кДж
2. Расход тепла
2.1. С суспензией при :
а) с осадком Ca(OH) 2
кДж,
где кДж / кг*град теплоемкость осадка Ca(OH) 2
Б) с раствором «известкового молока»
КДж,
где кДж / кг*град теплоемкость суспензии «известкового молока»
КДж
2.2. С недопалом
кДж /кг*град удельная теплоемкость недопала;
кДж /кг энтальпия воды при 90 0 С;
КДж
2.3. С парами воды:
Где кДж /кг энтальпия пара при 90 0 С;
КДж
2.4. Потери тепла в окружающую среду:
3 Дж,
где - коэффициент теплоотдачи, Вт /м 2 *град;
F боковая поверхность гасителя, м 2 ;
Градиент температур между стенкой гасителя и окружающим возд у хом;
Коэффициент перехода от часов к секундам.
Принимаем температуру стенки гасителя равной 50 0 С, температура окружа ю щего воздуха 20 0 С.
-.
Размеры гасителя (принимаем):
м, м
М 2
Вт/м 2 *град
3 =77472,45 кДж
кДж
Из уравнения теплового баланса
4385214,9 кДж = (4180198,87 + 231,39 Х ) кДж
Откуда:
Кг
Тогда после испарения в растворе содержится:
- воды 11841,6-88 = 11753,6 кг, в том числе с недопалом уходило 815,84 кг воды и в суспензии 10937,76 кг.
Сводный тепловой баланс гасителя.
Таблица 3
Приход |
Расход |
||||
Статья |
кДж |
Статья |
кДж |
||
С известью |
170925 |
3,3 |
С суспензией |
3683842,45 |
84 |
С водой |
3774540 |
86 |
С недопалом |
389908 |
8,89 |
От экзотермической реакции |
403940,3 |
9,28 |
С парами воды |
233992 |
5,34 |
Теплота растворения Са(ОН) 2 |
35809,6 |
0,82 |
Потери тепла |
77472,45 |
1,77 |
Всего |
4385214,9 |
100 |
Всего |
4385214,9 |
100 |
КОНСТРУКТИВНЫЙ РАСЧЕТ АППАРАТА ГАШЕНИЯ ИЗВЕСТИ
- Исходные данные:
Часовая производительность: G 1 = 5000 кг/ч (СаО)
G 2 = 15050 кг/ч (Н 2 О)
Угол наклона барабана: α = 0,5 0
Диаметр барабана: D б = 2,2 м
Число оборотов барабана: n = 3 ÷ 4 об/мин (принимаем)
Коэффициент заполнения: φ = 0,248 (принимаем)
Плотность материала:
где Х 1 = 0,07 вес по условию количество СаО в недопале
Кг/дм 3 плотность материала в барабане известегасителя
- Расчетная длина барабана известегасителя:
где Q = 0,6 коэффициент, зависящий от диаметра барабана;
n = 3 ÷ 4 об/мин = об/с число оборотов барабана в секунду.
Время пребывания материала в барабане:
*φ,
где V б объем барабана,
G ср средняя масса материала, проходящего через барабан, кг/с
Применяемые в производстве приготовления известкового молока гасители имеют длину барабана от 12 до 15 м и диаметр от 1,8 до 2,5 м, т.о. объем барабана гасителя с размерами:
min D б = 1,8 м, L б = 12 м,
max D б = 2,5 м, L б = 15 м
равен м 3
Средняя масса материала, проходящего через барабан:
кг/с
Время пребывания материала в гасителе:
С.
Тогда, длина барабана:
- при n = 0,05 об/с
L б = 0,6*0,05*2,2*7443,6* tg 0,5 = 4 ,3 м
- при n = 0,067 об/с
L б = 0,6*0,067*2,2*7443,6* tg 0,5 = 5,75 м
По чертежу длина барабана известегасителя 8,5 м, что приемлемо, так как гас и тель по условиям эксплуатации работать будет с крупными комками извести и целес о образно увеличить время гашения.
- Мощность, необходимая для вращения барабана гасителя:
* φ ,
где A=k 1 *k 2 *k 3 ,
k 1 =1 коэффициент диаметра барабана (при D б ≤ 2,2 м);
k 2 =1 коэффициент, учитывающий степень заполнения барабана и плотность су с пензии;
k 3 = 1,1 коэффициент, учитывающий крупность кусков извести;
n число оборотов барабана, об/мин.
=0,95 к.п.д. двигателя (принимаем)
кВт
ЗАКЛЮЧЕНИЕ
Аппарат гашения имеет следующие технические характеристики.
Тип |
АИ-2,2 |
Массовая подача по CaO , т/сут |
120 |
Частота вращения, мин -1 |
3-4 |
Редуктор |
1ЦГУ-250-40-21У1 |
Диаметр барабана |
1800 |
Длина барабана |
8500 |
Электродвигатель |
|
Мощность, кВт |
7,5 |
Частота вращения, мин -1 |
1000 |
По произведенным расчетам можно сделать вывод, что аппарат гашения удовл е творяет принятым на производстве нормам и стандартам и является неотъемлемой ч а стью в производстве известкового молока.
СПИСОК ЛИТЕРАТУРЫ
- Зайцев И. Д., Ткач Г. А., Стоев Н. Д. Производство соды. М.: «Х и мия» 1986 г.
- Расчеты по технологии неорганических веществ. Под. ред. П. В. Дыбиной, М.: «Высш. шк.» 1967 г.
- К.Ф. Павлов, П.Г. Романков, А.А. Носков «Примеры и задачи по курсу проце с сов и аппаратов химической технологии». М.: «Химия», 1976 г.
- Анурьев В. И. Справочник конструктора машиностроителя. Том 1. М.: «М а шиностроение» 1999 г.
- Табунщиков Н. П. Производство извести. М.: «Х и мия» 1974 г.
- Монастырёв А. В. Производство извести. М.: Стройиздат, 1972 г.
- Н.А. Колузин, В.Н. Соколов, А.Я. Шапиро «Примеры и задачи по курсу обор у дования заводов химической промышленности». М. Л.: «Машиностроение», 1966 г.
- А.С. Криворот «Конструкция и основы проектирования машин и аппаратов х и мической промышленности». М.: «Машиностроение», 1976 г.
- Рабочая инструкция аппаратчика гашения извести: РИ-38-006-2002, ОАО «АВИСМА».
Изобретение относится к сахарной промышленности, в частности к технологии известково-углекислотной очистки сахарсодержащих растворов. Способ предусматривает гашение извести водой в соотношении 100 мас.ч. извести к 105-115 мас.ч. воды до полной гидратации извести с образованием известковой пасты, которую затем охлаждают и смешивают с диффузионным соком с температурой 40-55°С. Известковое молоко очищают от неразгасившихся частиц на вибросите и гидроциклонах. Неразгасившиеся частицы, отделенные на вибросите, промывают водой в количестве 1-5% к массе обожженной извести и полученный промой смешивают с известковым молоком, подаваемым в гидроциклоны. Изобретение обеспечивает предотвращение разложения сахара в процессе приготовления известкового молока и улучшает качество известкового молока. 1 ил.
Рисунки к патенту РФ 2332467
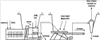
Изобретение относиться к сахарной промышленности, в частности к технологии известково-углекислотной очистки сахарсодержащих растворов.
Известен способ получения известкового молока для очистки сахаросодержащих растворов, включающий гашение извести водой, имеющей температуру 80-95°С, в соотношении 100 мас.ч. извести и 80-100 мас.ч. воды до образования пушонки, ее охлаждение до 80-95°С и смешивание с определенным количеством воды, имеющей температуру 60-85°С, до получения известкового молока с заданной плотностью .
Недостатки известного способа: использование большого количества чистой воды для приготовления известкового молока и получение известкового молока с недостаточно высокой активностью.
Ближайшим аналогом предложенного способа является способ получения известкового молока для очистки сахаросодержащих растворов, предусматривающий гашение извести водой, имеющей температуру 80-95°С, в соотношении 100 мас.ч. извести и 62-100 мас.ч. воды до образования рыхлой сыпучей массы с последующим ее охлаждением, при этом для получения суспензии в рыхлую сыпучую массу добавляют сахаросодержащий раствор (промои, разливы) с содержанием сахарозы 0,5-15% и температурой 60-85°С, причем процесс ведут при охлаждении до 80-85°С и полученную суспензию подвергают очистке от примесей .
Недостатком известного способа является то, что он не обеспечивает достаточно высокую степень гашения извести, приводя к разложению части сахарозы, содержащейся в сахарных растворах, используемых для смешивания с гашеной известью с попаданием вредных для сахарного производства продуктов распада сахарозы в очищаемый сок, причем использование указанных сахаросодержащих растворов температурой 60-85°С не обеспечивает получение известкового молока с достаточно высокой активностью.
Технический результат изобретения заключается в предотвращении разложения сахара в процессе приготовления известкового молока и улучшении качества известкового молока.
Технический результат достигается тем, что способ получения известкового молока для очистки сахаросодержащих растворов предусматривает гашение извести путем смешивания ее с водой, охлаждение гашеной извести, ее смешивание с сахаросодержащим раствором и очистку известкового молока от неразгасившихся частиц на вибросите и на гидроциклонах. Причем известь и воду используют в соотношении 100 мас.ч. извести и 105-115 мас.ч. воды и процесс ведут до образования известковой пасты, при этом из сахаросодержащих растворов для смешивания с гашеной известью используют диффузионный сок с температурой 40-55°С, при этом неразгасившиеся частицы, отделенные на вибросите при очистке известкового молока, промывают водой в количестве 1-5% к массе обожженной извести и полученный промой смешивают с известковым молоком, подаваемым в гидроциклоны.
Изобретение поясняется чертежом, на котором изображена схема процесса.
Способ получения известкового молока для очистки сахаросодержащих растворов осуществляют следующим образом. Перед гашением в известегасителе 1 негашеную известь смешивают с водой, имеющей температуру 80-95°С, в соотношении 100 мас.ч. извести и 105-115 мас.ч. воды и перемешивают в течение 10-20 мин, что достаточно для более полного гашения извести и образования известковой пасты. Во время перемешивания известковая паста нагревается до температуры более 100°С, с последующем ее охлаждением до температуры 80-95°С. Полученную известковую пасту смешивают с диффузионным соком, содержащим 10-15% сахарозы при температуре 40-55°С в смесителе 2, снабженном ситом для отделения крупных неразгасившихся частиц, что проходит без термического разложения сахара, так как в известковой пасте незначительное количество непогашеных частиц СаО в отличие от извести-пушенки. Также при смешивании в смесителе 2 диффузионного сока температурой 40-55°С с известковой пастой происходит отделение неразгасившихся частиц размером 8-10 мм, а также создаются благоприятные условия для растворимости образовавшегося во время гашения Са(ОН) 2 , так как сок, подаваемый на смешивание, имеет более низкую температуру, чем в известном способе; такая температура обусловлена обычной температурой сока, выходящего из диффузионного аппарата, при экстракции сахарозы из свекловичной стружки. Таким образом получают молоко требуемой плотности 1,16-1,22 г/см 3 .
Полученное известковое молоко подвергают очистке на вибросите 3 от неразгасившихся частиц, которые промывают водой в количестве 1-5% к массе обожженной извести и полученный промой смешивают с известковым молоком. Это позволяет смыть с частиц известковое молоко и сахарозу, отделить неразгасившиеся частицы средней фракции. Полученное таким образом известковое молоко после очистки на гидроциклонах 4 забирается на очистку сахаросодержащих растворов.
Пример 1. Получают известковое молоко для очистки сахарных растворов плотностью 1,16 г/см 3 . Для этого проводят гашение 311 г негашенной извести, смешивая ее с 326,5 г воды, имеющей температуру 80°С, в соотношении 100 мас.ч. извести и 105 мас.ч. воды, перемешивая 10 мин при охлаждении смеси проточной водой через рубашку. Полученную известковую пасту, имеющую температуру 85°С, разбавляют диффузионным соком, содержащим 13,8% сахара, сухих веществ 16,7%, с температурой 40°С в количестве 960 г. Полученную суспензию подвергают очистке от неразгасившихся частиц на сите, отделившиеся частицы промывают водой в количестве 10 г и полученный промой добавляют в известковое молоко. Далее полученную суспензию известкового молока плотностью 1,16 г/см 3 осветляют от примесей в лабораторном гидроциклоне под давлением 0,14 МПа.
В свежеприготовленном очищенном известковом молоке определяют содержание сахара, неразгасившихся примесей, активность известкового молока, а в промое после вибросит - содержание СаО. Так содержание сахарозы в 1,6 л известкового молока, полученного из 311 г СаО и разбавленного диффузионным соком, содержащим 13,8% сахара, сухих веществ 16,7%, с температурой 40°С, составило 131,2 г. Потери сахарозы при приготовлении известкового молока составили 0,7-0,8% к ее массе. Содержание примесей в свежеприготовленном очищенном известковом молоке составило 14 г/л. Содержание СаО в промое с вибросит составило 2,1 г. Активность известкового молока составила 89%.
Пример 2. Осуществляют процесс по известному способу. Готовят известковое молоко для очистки сахарсодержащих растворов плотностью 1,16 г/см 3 . Для этого гашение 311 г извести осуществляют 193 г воды, имеющей температуру 80°С, в соотношении 100 мас.ч. извести и 62 мас.ч. воды, перемешивают 10 мин, охлаждают до 80°С, затем полученную известь-пушонку разбавляют диффузионным соком, содержащим 13,8% сахара, сухих веществ 16,7%, с температурой 60°С в количестве 1240 г, одновременно охлаждая смесь до 85°С. Полученную суспензию подвергают очистке от неразгасившихся частиц на вибросите, дробят их до размера 0,2 мм и возвращают в известковое молоко. Полученную суспензию известкового молока плотностью 1,16 г/см 3 осветляют от примесей в лабораторном гидроциклоне под давлением 0,14 МПа. В свежеприготовленном очищенном известковом молоке определяют содержание сахара, неразгасившихся примесей, активность известкового молока, а в измельченных неразгасившихся частицах - активную СаО.
Так содержание сахарозы в 1,8 л известкового молока, полученного из 311 г СаО и разбавленного диффузионным соком, содержащим 13,8% сахара, сухих веществ 16,7%, с температурой 40°С, составило 166,3 г. Потери сахарозы при приготовлении известкового молока составили 2,9% к ее массе. Содержание примесей в свежеприготовленном очищенном известковом молоке составило 34,2 г/л. Активность известкового молока составила 83%.
Плотность известкового молока, получаемого по прототипу, как и по предлагаемому способу, 1,16 г/см 3 , но качественные показатели известкового молока были ниже. Так содержание примесей в очищенном известковом молоке из-за применения дробления при очистке известкового молока возросло в 2 раза, потери сахарозы при приготовлении известковго молока были в 3 раза больше, а активность ниже на 6%.
ФОРМУЛА ИЗОБРЕТЕНИЯ
Способ получения известкового молока для очистки сахаросодержащих растворов, предусматривающий гашение извести путем смешивания ее с водой, охлаждение гашеной извести, ее смешивание с сахаросодержащим раствором и очистку известкового молока от неразгасившихся частиц на вибросите и на гидроциклонах, отличающийся тем, что известь и воду используют в соотношении 100 мас.ч. извести и 105-115 мас.ч. воды и процесс ведут до образования известковой пасты, при этом из сахаросодержащих растворов для смешивания с гашеной известью используют диффузионный сок с температурой 40-55°С, при этом неразгасившиеся частицы, отделенные на вибросите при очистке известкового молока, промывают водой в количестве 1-5% к массе обожженной извести и полученный промой смешивают с известковым молоком, подаваемым в гидроциклоны.