Kalsiyum hidroksit: özellikleri ve uygulamaları. Kireç sütü hazırlanması.
Kireç - bağlayıcı, şaft veya döner tortul fırınlarda yüksek sıcaklıkta tavlama (1000 -1200 °C) ile elde edilir kayalar esas olarak kalsiyum karbonat CaCO3'ten (kireçtaşı, tebeşir, dolomit) oluşur.
Karbonat kayadaki kil safsızlıklarının içeriğine bağlı olarak, hava kireci (kil içeriği %8'den fazla değildir) veya hidrolik kireç (kayadaki kil içeriği %8 - 20'den fazla değildir) elde etmek mümkündür. Ayırt edici özellik hava kireci, sadece havada sertleşmesi ve su direnci olmamasıdır ve hidrolik kirecin daha hızlı sertleşmesi ve su direnci kazanmasıdır - en az iki hafta havada sertleştikten sonra sucul bir ortama yerleştirilebilir. Hava kireci en yaygın olanıdır ve üretimi sırasında sıcaklığın etkisi altında aşağıdakiler meydana gelir: Kimyasal reaksiyon CaCO 3 →CaO + CO 2
Aynı zamanda kalsiyum karbonat, karbondioksit (CO 2) ile kütlesinin %44'ünü kaybeder, hafif ve gözenekli hale gelir. Bu durumda elde edilen ürün, yumru sönmemiş kireçtir (ince gözenekli parçalar 5-10 cm boyutundadır). Gelecekte, topaklı sönmemiş kireç sönmemiş kireç tozu elde etmek için su ile söndürmeye veya ek öğütmeye tabi tutulur.
SÖNMÜŞ KİREÇ |
Parçalı kireci söndürmek için kullanılan su miktarına bağlı olarak aşağıdaki ürünler elde edilebilir:
- Sulu kireç ( tüy)
- kireç hamuru
- kireç sütü
Sulu kireç ( tüy)
Genellikle fabrika koşullarında (hidratörler) kirecin söndürülmesiyle elde edilen en ince beyaz toz sürekli eylem) olumsuzluk büyük miktar su (teorik olarak gerekli olandan biraz daha yüksek - kireç ağırlığının %50-70'i su). Kabartılarak söndürüldüğünde, kireç hacmi 2 - 2,5 kat artar.
Toplu yoğunluk - 400-450 kg / m3
Nem - en fazla %5
kireç hamuru
Su miktarı, yumru kirecin kütlesinin 3-4 katı olduğunda, kirecin suyla söndürülmesiyle elde edilir. Söndürme işlemi özel söndürme kutularında (yaratıcılar) gerçekleştirilir. Topak kireç kutuya, yüksekliğinin 1 / 3'ünden (tabaka kalınlığı yaklaşık 10 cm'dir) daha fazla yüklenmez, çünkü kireç sönme sırasında hacimde 2,5-3,5 kat artar. Hızlı söndürülen kireç, suyun aşırı ısınmasını ve kaynamasını önlemek için hemen bol miktarda su ile dökülür, yavaş söner - küçük porsiyonlarda, kirecin soğumadığından emin olun. 1 kg götürü kireçten kalitesine göre 2-2,5 litre kireç hamuru elde edilir. Kireç hamurundaki su içeriği standardize edilmemiştir. Tipik olarak, iyi yaşlanmış bir hamurda, suyun kirecin oranı yaklaşık 1:1'dir. Söndürme işleminin nihai olarak tamamlanması için gereken süre en az iki haftadır.
kireç sütü
Söndürme sırasında, su miktarı teorik olarak gerekli olan 8-10 katı aşıyor.
HIZLI TOZ KİREÇ |
toz olmanın avantajı sönmemiş kireç topaklanmadan önce, suyla karıştırıldığında bir alçı bağlayıcı gibi davranır: önce plastik bir hamur oluşturur ve 20-40 dakika sonra ele geçirir. Bunun nedeni, hamuru oluşturan karışım suyunun kısmen kirecin söndürülmesi için harcanmasıdır. Bu durumda kireç hamuru kalınlaşır ve plastisitesini kaybeder. Daha düşük serbest su miktarı nedeniyle, toz kireç esaslı malzemeler daha az gözenekli ve daha dayanıklıdır. Ek olarak, kireç sönme sırasında ısıtılır, bu da soğuk havalarda onunla çalışmayı kolaylaştırır. Kirecin kalitesine bağlı olarak, karıştırma için gereken su, kirecin ağırlığına göre %100-150'dir (ampirik olarak belirlenir).
Sönmemiş kireç tozunun kalitesinin en önemli göstergeleri şunlardır:
- Aktivite - söndürülebilecek oksitlerin yüzdesi.
- Sönmemiş tanelerin sayısı (yanmış veya yanmış).
az yanmış (ayrışmamış CACO 3) çok düşük bir pişirme sıcaklığında elde edilir, çünkü kirecin kalitesini düşürür. büzücü özelliklere sahip değildir.
Aşırı yanma, ateşleme sıcaklığı çok yüksek olduğunda meydana gelir. Yanmış taneler yavaş yavaş söndürülür ve zaten sertleşmiş malzemenin çatlamasına ve kırılmasına neden olabilir.
- Söndürme süresi. Söndürme süresine bağlı olarak, kireç türlere ayrılır:
- hızlı söndürme - 8 dakikaya kadar
- orta söndürme - 25 dakikaya kadar
- yavaş söndürme - en az 25 dakika
Bileşimin özelliklerine göre kireç 3 dereceye ayrılır.
Göstergenin adı |
Çeşitlilik |
||
1 |
2 |
3 |
|
Az değil, % |
90 |
80 |
70 |
11 |
14 |
KİREÇ UYGULAMASI |
İnşaat Kireç yapmak için kullanılır havanlar, kireç-puzolanik bağlayıcıların üretiminde, ısı yalıtım malzemelerinin üretiminde, suni imalatında taş malzemeler- silikat tuğlalar, gaz silikat blokları ve ayrıca boya bileşimlerinin üretiminde, kuru yapı karışımlarının üretiminde: sıva, yapıştırıcı, harç, duvar bileşimleri, dolgu maddeleri. |
|
Su arıtma ve su arıtma Kireç suyu yumuşatır, sudaki organik maddeleri çökeltir ve ayrıca asidik doğal ve atık suyu nötralize eder. |
|
|
Tarım Toprağa kireç ilave edildiğinde tarım bitkilerine zararlı asitlik ortadan kalkar. Toprak kalsiyum ile zenginleştirilir, toprağın işlenebilirliği iyileştirilir, humusun çürümesi hızlanır, uygulama ihtiyacı belirgin şekilde azalır. büyük dozlar azotlu gübreler. Hayvancılık ve kümes hayvancılığında, hidratlı kireç, hayvanların beslenmesindeki kalsiyum eksikliğini gidermek ve ayrıca çiftlik hayvanlarının genel sağlık koşullarını iyileştirmek için üst pansuman için kullanılır. |
|
Kireç Güvenliği Her türlü hava kireci oldukça güçlü bir alkalidir. Bu nedenle, onunla çalışırken, cildin açık bölgeleriyle ve özellikle solunum yolları ve gözlerle kirecin temasını önleyecek önlemler almak gerekir. Sönmemiş kireç özellikle tehlikelidir. Havadaki kireç tozu konsantrasyonu 2 mg/m3'ü geçmemelidir. |
OOO "GeoStyle" +7 495 663 93 93 teklif sulu kireç Kireç derecesi
84,39
68,04
67,32
71,0
5,80
2,98
1,0
2,7
Nem, %
0,87
0,36
0,5
0,28
öğütme inceliği:
Kalan partiküller elek No. 02,% ile elek üzerinde
0,19
1,48
0,0
0,0
Geri kalan partiküller elek No. 008,% ile elek üzerinde
1,28
9,20
1,0
0,31
OOO Müşterileri için "GeoStyle" teklifleri
katkı maddesi içermeyen 2. sınıf yüksek kaliteli öğütülmüş hızlı kireçlenmiş kireç
JSC "Kireç Üretim Tesisi" (Vladimir bölgesi) tarafından üretilmiştir
Zemin sönmemiş kirecin kalite göstergeleri
GOST 9179-77
JSC "Kireç bitkisi"
Göstergenin adı |
Analiz sonucu |
Çeşitlilik |
ikinci |
80,10 |
|
içermek MgO, % |
2,34 |
Söndürme hızı, min. |
|
Hidratlı su, % |
1,5 |
Söndürme sıcaklığı, o C |
90 |
Dağılım: |
|
02 numaralı elek üzerindeki kalıntılar, % |
1,5 |
008 numaralı elek üzerindeki kalıntılar, % |
15 |
Sayfa 1
Kireç özel söndürme tamburlarında ufalanıp söndürüldükten sonra doğrudan fabrikada hazırlanan kireç sütü, kuru karışım açısından %25 CaO oranında hammaddeye kurutulması ve pişirilmesi sırasında gerekli mekanik mukavemeti kazandırmak için dinas kütlesine ilave edilir. .
Limonlu süt olmalı spesifik yer çekimi 1045 - 1060, 1 litre kireç sütündeki CaO 56 - 75 g kireç içeriğine karşılık gelir.
Kireç sütü konsantre süt tankına girer ve 2NP pompaları tarafından NF tipi pompalarla askıya alınmış halde tutulduğu tanklara pompalanır. Aynı pompalar, dozlama için kireç sütü sağlar.
Karbürün bozunması sırasında jeneratörde elde edilen kireç sütü, çöken çamuru merkezi tahliye tertibatına hareket ettiren bir sıyırıcı karıştırıcı ile sürekli hareket haznesine (5) girer. Kireç çamuru daha sonra özel bir pompa ile çöktürme çukurlarına pompalanır. Hazneden (5) soğutucuya (4) geçen sudaki berrak kalsiyum hidroksit çözeltisi, kayıplarını telafi etmek için bir miktar tatlı suyun eklendiği basınç tankına (3) geri döner.
Kireç sütü (%10'luk çözelti), mekanik karıştırıcılarla donatılmış özel tanklarda sönmüş kireçten hazırlanır. İçin sürekli çalışma atık su arıtımının yapıldığı bölüm, sırayla çalışan en az iki kireç sütü tankı kurmak gerekir. Limonlu süt servis edilir gerekli miktar Nötralize edilecek atık suyun içinden aktığı reaksiyon odasına. Kireç sütünün iyi karışmasını sağlamak için kanalizasyon 30 - 40 rpm'de çalışan mekanik karıştırıcılar kullanılmalıdır.
2008 yılında yapılan işler
Kireç sütünün hazırlanması - Rapor, Kimya bölümü, - 2008 - Soda külü üretimi Kireç sütünün hazırlanması. Sodada Limon Sütü Gerekli...
Kireç sütü hazırlanması. 2NH4C1 Ca OH 2 CaCl2 2NH3 2H2O reaksiyonu ile amonyum klorürden amonyak rejenerasyonu için soda üretiminde gerekli olan kireç sütü, kirecin fazla su ile söndürülmesiyle elde edilir CaO H2O Ca OH 2 Ca OH 2 suda az çözünür ve artan sıcaklık, çözünürlük azalır.
0 C'de 100 g H2O başına 0.185 g çözünür ve 100 C'de 100 g H2O başına sadece 0.077 g çözünür. Bu nedenle, amonyum klorürün ayrışması için homojen bir çözelti değil, kireç sütü adı verilen su içinde Ca OH 2 süspansiyonu kullanılır. Kireç sütündeki askıda kalsiyum hidroksit konsantrasyonu mümkün olduğunca yüksek olmalıdır, çünkü kireç sütü ile amonyağın rejenere edildiği damıtma bölümüne ne kadar az su giderse, bu suyu ısıtmak için o kadar az buhar ısısı kullanılacaktır. rejenerasyon süreci.
Mümkün olan maksimum kireç sütü konsantrasyonu viskozitesi ile sınırlıdır.Çok viskoz süspansiyonun taşınması, kirliliklerden arındırılması ve dozlanması zordur. Süspansiyonun viskozitesi, yalnızca süspansiyon halindeki Ca OH2 konsantrasyonuna değil, aynı zamanda sıcaklığa da bağlıdır. Sıcaklık arttıkça viskozite azalır. Bu nedenle, 90 ° C'lik yüksek bir sıcaklıkta kireç sütü elde edilir; bu, söndürme için sıcak su kullanılmasının yanı sıra söndürme reaksiyonunun kendisi sırasında ısının serbest bırakılmasıyla sağlanır.
Bu ısı, kireç sütünün sıcaklığını yaklaşık 75°C artırabilir, ancak pratikte ısının önemli bir kısmı söndürme işlemi sırasında suyun buharlaşmasına ve ısı radyasyonuna kaybedilir. Bu nedenle, söndürme için 60-65 C'ye ısıtılmış su kullanılarak 90-95 C sıcaklıktaki kireç sütü elde edilebilir.Kireç sütünün kalitesi, kirecin kalitesinden önemli ölçüde etkilenir. Örneğin, karbonat hammaddelerinin pişirildiği sıcaklık önemlidir; ne kadar yüksek olursa, ortaya çıkan kireç o kadar yavaş söndürülür ve daha az dağılmış kireç sütü elde edilir.
Ateşleme sıcaklığı 1350 C'nin üzerinde çok yüksekse, pratik olarak artık su ile söndürülmeyen kireç elde edilir. Kireçte bulunan safsızlıklardan kalsiyum sülfat, sönme süresi üzerinde en büyük etkiye sahiptir. Kireç sütünün yüksek derecede dağılması, yalnızca amonyum klorürün bozunma hızı için önemli değildir.
Oldukça dağınık bir süspansiyonun katmanlaştırılması daha zordur, homojenliğini daha iyi korur, bu da dozlama sırasında önemlidir, boru hatlarını tıkamaz ve pompaları ve iletişimi daha az yıpratmaz. Kireç sütünün yaklaşık bileşimi aşağıdaki gibidir Ca OH 2 . 200 - 250 yok Mg OH 2 1 - 2 g l CO2-3 7 - 14 n.d. CaSO4 1 - 3 g l SiO2 suda çözünmeyen safsızlıklar HCl 10 - 20 g l R2O3 5 - 8 g l Yoğunluk. sıcak su ve kireç sütünün büyük parçalardan ve küçük nedopal, perekal ve diğer çözünmeyen safsızlıklardan arındırılması.
Tek tek cihazlar için malzeme akışlarının hareketi, Şek. 8. Çalışma hunisinden 2 kireç, bir tepsi besleyici 1 tarafından dönen bir tambur söndürücüye 3 beslenecektir, burada ısıtılmış su ve yıkama suyu yıkandıktan sonra kirecin atık safsızlıkları, zayıf kireç sütü aynı anda girer. 8 Şek. 8 kireç sütü hazırlamak için teknolojik şema 1 - tepsi besleyici 2 - çalışma hunisi 3 - tambur - söndürücü 4 - kondansatör 5 - kaba alt kısım için ayırma tamburu 6 - konveyör 7 - ayırma tamburu 8 - burgu 9 - ıslak öğütme bilyalı değirmen 10 - ham zayıf karıştırıcı sütü 11 - titreşimli elek 12 - saflaştırılmış zayıf kireç sütü karıştırıcısı 13 - atık çamur karıştırıcısı 14 - sınıflandırıcı 15 - konsantre kireç sütü karıştırıcısı. Söndürücüde (3), kireç söndürülür ve çeşitli boyutlarda alt kısım, perekal ve diğer sönmemiş kireç parçacıklarının bir karışımı ile kireç sütü oluşturulur.
Kireç sütü kirliliklerle birlikte söndürücüden 3, 40 mm delikli bir elek olan kaba nedopal için ayırma tamburuna 5 gelir. Büyük nedopal için ayırma tamburu, emicinin bir devamıdır, onunla birlikte döner ve büyük nedopal parçalarını kireç sütünden ayırmaya yarar. Tamburdaki deliklerden geçen kireç sütü, daha fazla temizlik için ince nedopal için ayırma tamburuna 7 girer.
Tamburun ucunda 40 mm'den daha büyük olan büyük altlık parçaları sıcak suyla yıkanır, konveyöre 6 beslenir ve yeniden kireçlenme için kireç fırınlarına aktarılır.
Büyük nedopal için ayırma tamburu (5), yangın söndürücüde oluşan buharı çıkarmak için iki egzoz borusuyla donatılmış bir mahfaza içine alınır. Bir boru, söndürücüden gelen buharın yoğuşarak söndürme için kullanılan suyu ısıttığı kondenser 4'e gider ve ikinci boru, kondenserin onarımı veya temizlenmesi durumunda atmosfere yönlendirilir.mm, 2 mm'den büyük partiküller kireç sütünden ayrılır. Kireç sütü, bir elekten geçerek, ayırma tamburunun kapatıldığı muhafazanın koni şeklindeki alıcısına girer ve buradan safsızlıklardan son temizlik için sınıflandırıcıya (14) gider. Kireç sütü mikseri amacına göre 15 l daha - damıtma bölümüne.
Ayıklama tamburunda kalan 2 mm'den büyük katı parçacıklar, tambur döndüğünde, kademeli olarak hareket eder ve yardımıyla ıslak öğütme bilyalı değirmeni 9'a beslendikleri vidaya 8 boşaltılır. Perekal parçaları öğütülürken açılan değirmende kireç söndürülür.
Değirmende elde edilen zayıf kireç sütü, safsızlıklarla birlikte, nedopalın yıkanması sırasında oluşan zayıf kireç sütünün de boşaltıldığı karıştırıcıya 10 akar.
Çamurdan temizlemek için mikserden zayıf kireç sütü pompalanır 10 santrifüj pompası Titreşimli elekten gelen çamur, atık çamur karıştırıcısına (13) girer ve arıtılmış zayıf kireç sütü, arıtılmış zayıf sütün (12) karıştırıcısına girer ve buradan pompanın onu söndürücüye iletir.
Sınıflandırıcıdan (14) ve titreşimli elekten (11) gelen çamur, karıştırıcıda (13) damıtıcının atık sıvısı ile seyreltilir ve santrifüjlü bir pompa ile atık sıvı akümülatörüne - sözde beyaz deniz - pompalanır. Kireç sütü ayırma teknolojik modunun normları, bunların düzenlenmesi ve kontrolü Kireç sütünün kalitesini karakterize eden ve damıtma bölümünün normal çalışmasını sağlayan en önemli düzenlenmiş göstergeler Ca OH 2 veya serbest CaO konsantrasyonu ve sıcaklığıdır. Süt.
Soda fabrikalarında, kireç sütündeki serbest CaO konsantrasyonu, sütün olağan titrasyonu ile belirlendiğinden süt titresi olarak adlandırılır. hidroklorik asit. Üretim için, kireç sütündeki Ca OH 2 içeriğinin mümkün olduğunca yüksek olması gerekir, çünkü bu damıtma sıvısının hacmini azaltır ve sonuç olarak damıtma bölümünün verimliliği ve buhar tüketimi ve buhar tüketimi artar. Damıtıcının atık sıvısı ile kireç ve amonyak kaybı azaltılır.
Bununla birlikte, süspansiyonun viskozitesini artıran aşırı yüksek bir Ca OH2 konsantrasyonu, söndürücünün çalışmasında ve sütün safsızlıklardan arındırılmasında zorluklar yaratır. Uygulama, süt titresinde izin verilen Ca OH 2 konsantrasyonunun 200-250 n aralığında olabileceğini göstermiştir. e.Ayrıca süt titresindeki dalgalanmalar damıtma bölümünde sütün dozajını kontrol etmeyi zorlaştırdığı ve damıtıcının atık sıvısındaki kireç ve amonyak kaybını artırdığı için minimumda tutulmalıdır.
Atık sıvıda, serbest CaO 1-2 n dalgalanmalarına izin verilir. ölmek. bir normal bölünme içinde. Damıtma bölümünün aparatında kireç sütü yaklaşık 4 kat seyreltilir. Bundan, süt titresindeki dalgalanmaların 4 N'yi geçmemesi gerektiği sonucu çıkar. e. Sütün titresi, söndürme için sağlanan su miktarı değiştirilerek düzenlenir. Titre dalgalanmaları nispeten büyük kaplarda - kireç sütü karıştırıcılarında - dengelenir.
Söndürücüye verilen kireç miktarı, soda külü, kostik, su arıtma vb. tüketen dükkanlar tarafından kireç sütü tüketimi ile belirlenir. İlk yaklaşımda kireç sütündeki Ca OH 2 konsantrasyonu yoğunluğu ile değerlendirilebilir, Bu, operatör tarafından doğrudan mağazada kolayca ölçülebilir. Daha fazlası için kesin tanım her 30 dakikada bir atölye laboratuvarında serbest CaO içeriğini analiz edin. Yüksek bir serbest CaO titresine sahip kireç sütü elde etme olasılığı, elde edilen sütün sadece konsantrasyona değil aynı zamanda sıcaklığa da bağlı olan viskozitesi ile sınırlıdır. Sıcaklıktaki bir artışla sütün viskozitesi azalır, safsızlıklardan arındırılması için koşullar iyileşir ve nakliyesi ve dozajı da kolaylaşır.
Bu nedenle, yüksek titreli süt elde etmek için kireç söndürmek gerekir. yükselmiş sıcaklık. Teknolojik rejimin normları, 85-95 C sütün son sıcaklığını sağlar. Bu sıcaklık, büyük ölçüde, söndürücüden çıkan su buharının yoğuşma ısısı ile ısıtılan, suyun söndürülmesi için sağlanan sıcaklığa bağlıdır.
Soda gazı soğutucusundan veya damıtma gazı soğutucusundan gelen atık su ısıtma için kullanılabilir. Teknolojik rejimin normları, kireç sütündeki CO32- içeriğini 7-12 n miktarında sağlar. e. Bu değer, pratik olarak NH4C1 ile etkileşime girmeyen sütteki CaCO3, işe yaramaz aktif olmayan kireç içeriğini, yani. sütün safsızlıklardan arındırılma derecesi.
Kireç sütünü ekonomik olarak makul sınırlara kadar arıtmak gerekir, çünkü saflaştırma derecesinin artmasıyla süreç daha karmaşık hale gelir. Kireç sütündeki CO32- içeriği normu bu makul sınırı gösterir. Absorpsiyon Soğurucunun amacı, tuzlu suyun kolon yıkayıcıdan amonyakla son doygunluğunu gerçekleştirmektir. Daha önce diğer tuzların safsızlıklarından saflaştırılmış 310 g l sodyum klorür içeren tuzlu su, amonyak ve ana sıvının vakum filtrelerinden sonra yeniden üretildiği damıtma kolonundan amonyak sağlanan emiciye girer.
Bikarbonat kalsinasyon fırınından çıkan amonyak ve karbon dioksit içeren gaz da absorbere girer. Amonyaklaştırma sırasında tuzlu su kalsiyum ve magnezyum tuzlarından yeterince temizlenmezse, istenmeyen yan reaksiyonlar meydana gelebilir Amonyak ve karbon dioksit, kalsiyum ve magnezyum tuzları ile etkileşime girerek, aparatın duvarlarında birikebilen kalsiyum karbonat ve magnezyum hidroksit çökeltileri oluşturur. ve boru hatları.
Tuzlu su temizleme rejiminin sistematik bir şekilde ihlali ile, aparatların ve boru hatlarının duvarlarında CaCO3 ve Mg OH 2 birikintileri, absorpsiyon bölümünün normal çalışmasını bozabilir. Bütün absorpsiyon prosesi esas olarak damıtma kolonundan absorbere giren gazların miktarına 1 ve damıtmaya giren tuzlu su miktarına bikarbonat kalsinasyon fırınına (2) bağlıdır, daha sonra absorpsiyon prosesinin düzenlenmesi akışın düzenlenmesinden oluşur. doymuş amonyak sıvısı gerekli konsantrasyona sahip olacak şekilde tuzlu su.
Absorpsiyonlu ayırmanın teknolojik şeması Absorbsiyonlu ayırmanın teknolojik şeması şunları sağlamalıdır: yüksek derece egzoz gazlarının amonyaktan arıtılması, bunun için bu gazların minimum miktarda amonyak içeren taze tuzlu su ile yıkanması gerekir. Karbondioksitin emilimi amonyaktan çok daha yavaştır, bu nedenle ekipman, belirli bir miktarda amonyak ve mümkün olan maksimum miktarda karbondioksiti emecek şekilde tasarlanmalıdır.
Taze tuzlu su öncelikle egzoz gazlarından amonyağı emmek için kullanılır. Tuzlu suyun yaklaşık %75-80'i basınç tankından 3, amonyak vakum filtrelerinin filtre bezinden geçen ve yaklaşık 0,5-1 NH3 içeren havadan emildiği filtreli hava yıkayıcı PVFL 4'e gelir. PVFL'den sonra, tuzlu su PGKL-2 7 kolonlarının ikinci gaz yıkayıcısına gider; burada amonyak, karbonizasyon bölümünün 10'a kadar NH3 içeren çıkış gazlarından emilir. Basınç tankı 3'ten kalan 20-25 taze saflaştırılmış tuzlu su, absorpsiyon gazı yıkayıcısı PHAB 1'e girer, burada amonyağın 5'e kadar NH3 içeren absorpsiyon bölümünün çıkış gazlarından emilir. Yol boyunca, egzoz gazlarında bulunan belirli bir miktar karbondioksit emilir. PVFL'den gelen gaz, vakum filtreleri üzerinde bir vakum oluşturan ve atmosfere salınan vakum pompasına (5) girer.
PHAB'den gelen gaz da vakum pompası 2'ye girer. En az 75 CO2 içerir, bu nedenle vakum pompası onu soda fırınlarından gelen karbondioksit ile karıştırmaya ve ardından karbonizasyona aktarır.
PGKL-2'den çıkan egzoz gazları atmosfere salınır. Şekil 8. Absorpsiyonlu ayırmanın tipik teknolojik şeması 1-absorpsiyonlu gaz yıkayıcı 2.5-vakum pompaları 3-basınç tankı 4-filtreli hava yıkayıcı 6-damıtma gazı soğutucusu 7-saniye kolonlu gaz yıkayıcı 8-ayırıcı-püskürtme kapanı 9 - aminize tuzlu su toplayıcı 1 0, 12 -sulama buzdolapları 11-ayaklı rezervuar 13-ikinci emici 14-birinci emici 1 14 ve ikinci emici AB-2 13'te. Çözünmeden ısıtılan tuzlu suyun ara soğutulması ihtiyacından iki emme aşaması neden olur ve NH3 ve CO2 etkileşimi ve damıtma gazı ile sağlanan su buharının yoğuşmasından.İlk emiciden sonra, tuzlu su 60-65 C'ye ısıtılır, sulama soğutucusunda 12 28-32 C'ye soğutulur, ardından ikinci emiciye girer, burada da yaklaşık 65°C'ye ısıtılır ve sonra amonyaklı tuzlu su toplayıcı CAP 9'a girmeden önce, sulama soğutucusunda 10 tekrar soğutulur. Tuzlu suyun yerçekimi ile sulama soğutucusuna akışını sağlamak için ikinci emici ve üzerinde duran cihazlar bir kaide - tank 11 üzerine yerleştirilir. Distilasyon bölümünden gelen gaz önce distilasyon gaz soğutucusu CHGDS 6'da soğutma suyu ile soğutulur ve kurutulur ve ardından separatör - sis kapanı 8'den geçtikten sonra ikinci ve birinci absorberler ardışık olarak tuzlu suya geçer ve burada amonyağın emildiği yer hemen hemen hepsi.
Amonyak ile birlikte, karbondioksitin çoğu gazdan emilir.
Emilmeyen gazlar PGAB 1'e gider. Damıtma gazı CHGDS'de soğutulduğunda, su buharı yoğunlaşarak 150-200 N'ye kadar bir kondensat oluşturur. e. amonyak ve karbondioksit.
Zayıf sıvılar olarak adlandırılan bu tür sıvılardan amonyak ayrı bir tesiste rejenere edilir.
NH3, CO2 ve H2O içeren ve 58-60°C'ye soğutulan sonuçtaki gaz genellikle ilk emiciye girer. Amonyaklı tuzlu suyun karbonizasyonu Sodyum bikarbonat oluşumu ile sonuçlanan amonyaklı tuzlu suyun karbon dioksit ile doyurulmasının karbonizasyon süreci, soda üretiminin ana sürecidir.
karbonizasyon bölümünde almak miktar ayarla Bölüme aktarılan sürekli bir malzeme akışı şeklinde sodyum bikarbonat içeren süspansiyon. Süspansiyonun kalitesi, içerdiği sodyum bikarbonat ürününün kalitesi ile belirlenir. Çoğu zaman, sodyum bikarbonatın kalitesi, fraksiyonel bileşimi ile değerlendirilir. Süspansiyonun kalitesinin tanımlayıcı değerlendirmesi, bu süspansiyonun standart koşullar altında filtrelenmesiyle elde edilen sodyum bikarbonatta kalan nem içeriğidir.
Karbonizasyon kolonunun çalışmasının değerlendirilmesi, boyutsuz bir teknik optimallik kriteri kullanılarak verilebilir. askıya almanın açıklığa kavuşturulmuş kısmı, n.d. wc - sodyum bikarbonatta kalan nem içeriği Sodyum bikarbonatın üretkenliği ne kadar yüksek ve üründeki artık nem ne kadar düşükse, karbonizasyon kolonu o kadar iyi çalışır, yani optimallik kriterinin mutlak değerini artırmak için çaba sarf etmek gerekir.
Karbonizasyon işleminin bir sonucu olarak, NaCl NH3CO2 H2O - NaHCO3 NH4C1 reaksiyonu ile oluşan çözeltiden sodyum bikarbonat çökelir. Bu reaksiyon, sodyum klorür ve amonyum bikarbonat etkileşiminin yalnızca nihai sonucunu karakterize eder. Gerçekte, karbonizasyon süreci çok daha karmaşıktır ve mekanizması henüz tam olarak aydınlatılamamıştır.
Karbonizasyon işlemi aşamalı olarak gerçekleştirilir. İlk olarak, amonyaklı tuzlu su, KLIK ön karbonizasyon kolonunda kireç fırın gazı ile muamele edilir, daha sonra gazların çökelme kolonlarından çıkan gazlarla PGKL-1 kolonlarının ilk gaz yıkayıcısında ve son olarak KL çökeltme kolonlarında alt kısma 65-75 CO2 karışık gaz ve orta kısımda - kireç fırınlarından gelen gaz. Karbonizasyonun ilk aşamasında, karbondioksitin çoğu amonyum karbamat 2NH3CO3 NH2COONH4'e bağlanır ve daha sonra NH2COONH4 H2O - NH4HCO3 NH3 tarafından hidrolize edilir ve bir HCO3 aşırı doymuş çözeltisi oluşur.
Daha sonra, NH4HC03 NaCl - NaHC03 NH4Cl reaksiyonu ile oluşan aşırı doymuş çözeltiden sodyum bikarbonat kristalleşir. Amonyaklı tuzlu suyun karbon dioksit ile doyma süreci ekzotermiktir. Çözeltinin gerekli karbonizasyon derecesini ve sodyum kullanımının kullanımını sağlamak için işlemin son aşamasında açığa çıkan reaksiyon ısısı uzaklaştırılmalıdır. Sıcaklık rejimi karbonizasyon kolonu, sodyum bikarbonat kristallerinin oluşum sürecini önemli ölçüde etkiler.
Büyük sodyum bikarbonat kristalleri elde etmek için doğru biçim Vakum filtrelerinin süzme yüzeyini tıkamayan ve süzme işleminde az çözünür olan , oluşum bölgesinde ve kristal büyümesinin ilk döneminde 60-72 C gibi nispeten yüksek bir sıcaklığın korunması gereklidir. Kristallerin daha fazla büyümesi sürecinde, sıcaklığın artık boyutları üzerinde önemli bir etkisi yoktur. Kristalizasyon işlemi, normal bir teknolojik rejimi korurken, kısa silindirler - variller şeklinde kristallerin oluştuğu çok küçük sodyum bikarbonat kristalleri şeklinde çekirdek oluşumu ile başlar. Kristalleşme sürecinin bozulmasıyla birlikte, uzun silindir şeklinde olan ve drus demetleri şeklinde iç içe büyüme oluşumuna eğilimli kristaller oluşur. Bu durumda, iğne benzeri kristaller ve şekilsiz parçalar şeklinde büyük miktarda ince parçacıklar salınır. Filtrasyon sırasında, bu tür kristaller daha yoğun hale gelir ve oluşan küçük hücrelerde çok fazla nem tutar, yani sodyum bikarbonattaki artık nem içeriği artar.
Karbonizasyon bölümünün teknolojik şeması Amonyaklı tuzlu su toplayıcı SAR'dan gelen amonyaklı tuzlu su, aynı zamanda 32-36 hacim içeren kireç fırın gazı ile beslenen KLPK'nın ön karbonizasyon sütununa girer. Tebeşir ateşlemesi sırasında CO2 ve 38-40 hacim. Kireçtaşı kalsinasyonu sırasında CO2.
KLPK'dan 42-46 C sıcaklıktaki sıvı, PGKL-1 kolonlarının ilk gaz yıkayıcısına gönderilir. KLPK ve çökeltme kolonlarından gelen gaz da buraya girer.
PGKL-1'de amonyak yakalanır ve KLPK'dan gelen karbonize gazla üflenir. Sıvının PGKL-1'den geçişi sırasında sıcaklığı 5-8 C yükselir. PGKL-1'den sonra sıvının ilave soğutulması için sıvının çökelme karbonizasyon kolonuna girdiği yerden bir ısı eşanjörü sağlanır. Kolonun alt kısmında 70-80 hacim karbon dioksit içeren karışık gaz ilk girişi ve orta kısımda - kireç fırını gazı ikinci girişi beslenir. Çökeltme karbonizasyon kolonundan gelen gaz PGKL-1'e gönderilir ve süspansiyon filtrasyon bölümüne gönderilir.
Karbonizasyon kuleleri, filtrasyon bölümüne sürekli bir bulamaç akışı sağlamak için seri olarak çalıştırılır. En yaygın olarak kullanılan seri, üçü çökeltme kolonu olarak çalışan ve biri ön karbonizasyon kolonu olan dört karbonizasyon kolonundan oluşur.
Karbonizasyon bölümü için donatım Karbonizasyon kolonu KL. Karbonizasyon bölümünün ana aparatıdır. KL, 3'e kadar çapa ve 27 m'ye kadar yüksekliğe sahip, bir dizi dökme demir varil veya çardan oluşan silindirik içi boş bir sütundur. Yukarıdan 5 numaralı armatür ve kolon aracılığıyla, karbonize edilecek çözelti PGKL-1'den, alttan 2 numaralı bağlantı ve ortada 9 numaralı bağlantı aracılığıyla gelir. karbon dioksit. Çalışma sırasında, kolon belirli bir sabit seviyeye kadar bir çözelti ile doldurulur. Şekil 9. 2680 mm karbonizasyon kolonu 1-tambur tabanlı 2-gaz giriş bağlantısı 3-soğutma tamburu 4-absorpsiyon tamburu 5-sıvı giriş rakoru 6-ayırma tamburu 7-gaz çıkış rakoru 8-kabarcık kolonu 9-gaz giriş rakoru 10 süspansiyon için çıkış.
Karşı akış ilkesinin uygulanması, sıvının gazla kolonun yüksekliği boyunca boylamasına karıştırılmasıyla engellenebilir. Bu karışmayı en aza indirmek için, kolonun ayrı fıçıları (4) arasına pasolar veya kabarcıklı plakalar (8) yerleştirilir Plaka, gaz ve sıvı arasındaki temas yüzeylerinden oluşan bir taban (2) ve onu kaplayan bir kapaktan (1) oluşur.
Kolonun üst kısmına, gazın sürüklediği sıvı sıçramalarını ayırmak için tasarlanmış ve kolondaki sıvı seviyesini izlemek için su gösterge camlarına sahip iki boş ayırma varili (6) monte edilmiştir. Kolonun üstü, gaz çıkışı ve bir emniyet valfi takmak için bir bağlantı 7 bulunan bir kapakla kapatılmıştır.
Karbonizasyon kolonunun tabanında, küresel tabanlı bir varil tabanı 1 ve içinden bir sodyum bikarbonat süspansiyonunun çıkarıldığı ve 1. girişin karışık gazının bir kompresör tarafından sağlandığı bağlantı parçaları 10 ve 2 vardır. Kolonun fıçıları ve köpüren tepsileri dökme demirden yapılmıştır. 6 mm kalınlığındaki soğutulmuş varillerde ince duvarlı borular karbon çelik veya 0,5 Ni, 0.4 Mn, 3.3 C ve 0.4 Cr içeren özel dökme demirden.
İş bitimi -
Bu konu şunlara aittir:
Soda külü üretimi
On sekizinci yüzyılın sonuna kadar, esas olarak Macaristan, Mısır ve Afrika'nın diğer bölgelerindeki doğal yataklardan ve deniz külünden çıkarıldı ... O zamanın sodası saflıkla ayırt edilmedi. 1775 yılında Fransız Akademisi... Leblanc'ın yöntemi Leblanc'ın yöntemi, sülfürik asit sülfat ile sofra tuzunun hazırlanmasından oluşuyordu ve ...
Eğer ihtiyacın varsa ek malzeme Bu konuda veya aradığınızı bulamadıysanız, çalışma veritabanımızda aramayı kullanmanızı öneririz:
Alınan malzeme ile ne yapacağız:
Bu materyalin sizin için yararlı olduğu ortaya çıktıysa, sosyal ağlarda sayfanıza kaydedebilirsiniz:
17
FEDERAL EĞİTİM AJANSI
PERM DEVLET TEKNİK ÜNİVERSİTESİ
BEREZNIKOVSKI ŞUBESİ
TEKNOLOJİ VE ÜRETİM MEKANİZASYONU BÖLÜMÜ
KURS PROJESİ
DERS İÇERİSİNDE: « TEKNOLOJİK SÜREÇLER VE ÜRETİM»
KONU: "Kireç m üretiminde kireç söndürme aparatının hesaplanması hakkında OJSC AVISMA'da loca»
Tamamlandı: Sanat. gr. ATP-01(c) Gavryushin K.G.
Kontrol edildi: st. öğretmen Demin D.Yu.
Berezniki 2005
sayfa |
|
GİRİİŞ |
|
ÖN SOĞUTUCU MALZEME DENGESİ NIA |
|
ÖN SOĞUTMA ODASI ISI DENGESİ |
|
ÖN ODA TEKNOLOJİK HESAPLAMASI SOĞUTMA |
11 |
ÇÖZÜM |
12 |
KAYNAKÇA |
13 |
GİRİİŞ
Sönmüş kireç, üzerine belirli bir miktar su verilerek elde edilir. a kıyılmış kireç, bunun sonucunda toz (kabartma), kireç t hamur veya kireç sütü.
Kireç sütü, bir miktar su katılarak oluşturulur, pr e teorik olarak gerekli olanın on katından fazla. Karmadaki ortalama parçacık boyutu e kireç sütündeki nii bir mikrona eşittir. Daha da artmasıyla ve su kalitesi söndürme ürünü hakkında elek kireçli suyun adıdır.
Kireç sütü kalitesi için temel gereksinimler.
Kalsiyum hidroksit, etkileşimle elde edilen bir süspansiyondur. t su ile çiş kalsiyum oksit.
Yoğunluk Ca(OH) 2 konsantrasyona ve ağırlığa bağlı olarak yakl. e bu 1,15 1,30 g/cm arasında dalgalanıyor 3 , özgül ağırlık 1,2 g/cm 3. Suda, Ca (OH) 2 zayıf çözünür ve artan sıcaklıkla çözünürlük azalır. Mümkün olan maksimum kireç sütü konsantrasyonu, viskozitesi ile sınırlıdır. ve h kemik süspansiyonu sadece asılı Ca(OH) konsantrasyonuna bağlı değildir 2 ama aynı zamanda sıcaklıkta. Bu nedenle kireç sütü yüksek sıcaklıklarda elde edilir. ve turlar (90 0 С).
Süspansiyon Ca(OH) 2 güçlü bir alkalidir, ikinci sınıf tehlikeli hakkında şti. Proteinleri çözerek cilt üzerinde yakıcı bir etkisi vardır. Aerosollerin solunması s üst solunum yollarının mukozalarında değişiklikler, ron vardır ve kal bronşit. Vb e 0.5 mg / m2 aerosol şeklinde spesifik - izin verilen konsantrasyon 3 . Görme kaybına neden olduğu için gözlere girmek tehlikelidir. Bunlar tehlikeli özellikler artan süt sıcaklığı ile artar. Kireç sütü olan işçilerin tulumları olmalıdır: lastik çizme, kanvas takımlar, gözlükler, kasklar ve eldivenler.
OJSC AVISMA'da kalsiyum hidroksit, zararlı maddeler atık gazlar ve endüstriyel atıklar.
TEKNOLOJİK ÜRETİM ŞEMASI TANIMI
Kireç sönmesi reaksiyonla ilerler:
CaO + H20 \u003d Ca (OH) 2 + 15.93 kcal.
Söndürme için verilen su miktarı değiştirilerek, de kireç tozu (ince toz), kireç macunu (kalın e sıvı kütlesi), kireç sütü sulu süspansiyonu Ca(OH)2.
Kalsiyum oksitin hidrasyonu tersinir bir reaksiyondur, örneğin içinde içindeki su buharının sıcaklığına ve basıncına bağlıdır. ile kesme ortamı. ayrışma esnekliği CaO ve H 2 O üzerinde Ca (OH) 2 ulaşır atmosferik basınç sıcaklıkta y yeniden 547 0 C, bir a Ca oksidin ko-hidratı, daha düşük sıcaklıklarda bile kısmen ayrışabilir. Sürecin doğru yönde ilerlemesi için gerekli e su buharının esnekliğini arttırmayı amaçlar. Ca (OH) 2 ve izin verilmez çok yüksek sıcaklık. Aynı zamanda, söndürülmüş hipotermi ve h önemli ölçüde yol açabileceğinden a Söndürme sürecini yavaşlatın. Söndürme işlemi, suyun sıcaklığından ve reaksiyona giren karışımdan önemli ölçüde etkilenir. Reaksiyon dizisi ve Ca (OH) 2 oluşumu ekzotermik, aşırı nem ekshalasyonla ısıtılır e hafif ısı.
Sıcaklık arttıkça, çöken kalsiyum oksit hidrat a sönmemiş kireç parçalarının yüzeyini çökeltir ve sarar. Sonuç olarak duruyor hakkında sönmemiş kirecin suyla teması ve söndürme işlemi durur.
Söndürme durdurulduğunda suyun sıcaklığı düşer, çözülür o Hazırlık Ca (OH ) 2 artar, film Ca(OH)2 sönmemiş kireç parçaları üzerinde tekrar çözüm ben sona erer ve söndürme işlemine devam edilir. Bu nedenle, kireç ile söndürme işlemi hakkında "kendi kendine" fenomeni tarafından gerçekleştirilir. R kabiliyet." Bu nedenle, yürütülürken daha iyi sonuçlar elde edilir. hakkında sabit sıcaklıktaki bir ortamda söndürme işlemi.
Kirecin aktivitesi kristallerin boyutuna bağlıdır. CaO ve ihlal derecesi kristal kafes. Pişirim sıcaklığı arttıkça kristalin boyutu ben yakalamalar artar, kristal kafesin bozulma derecesi azalır ve ile sönmüş kireç aktivitesi ve can atıyor.
Kirecin silikon, alüminyum, demir oksitleri ile etkileşimi ürünleri (ile ve Likatlar, alüminatlar, ferritler) kirecin etkisini azaltır hidrasyon için ti ile.
Söndürüldüğünde, bu safsızlıklar bir veya daha fazla su molekülünü kendilerine bağlayarak hidrosilikatlar, kireç haline gelmeyen kalsiyum hidroalüminatlar oluşturur. t inek sütü. Bu durumda hidrasyon işlemine şişme ve bu bileşiklerin jöleye geçişi eşlik eder. e figüratif durum.
Uzun süre havada kalırsa yanmış kireç bulunur. ve "pasiflik" olgusunu doğurur. Havada uzun süre kalmak, kendiliğinden g a havadaki nem pahasına. Kabuk çözünür Ca(OH)2 Kuso'da bulunan h kah kireç, nera'ya gider oluşturulabilir CaCO 3 ile , hangi izole eder CaO nem eyleminden.
2. Açıklama teknolojik süreç operasyonlarla
sönmemiş kireç yumru kireç kireçtaşı kavurma bölümünden, akış-taşıma şemasına (PTS) göre kireç hazırlama bölümü (MLC) sütüne taşınır.
Kireç CM-11B çeneli kırıcıda kırıldıktan sonra geri dönüşümlü olarak girer içinde konveyör, daha sonra 85810 mm ve 19000 mm uzunluğundaki konveyörler boyunca üç besleme kutusuna gönderilir (toplam kapasite yaklaşık 60 ton).
Besleme hunilerinden kireç, PKL-8-0 besleyiciler tarafından yüke taşınır de AI-1, 8M2 kireç söndürme aparatının keskin olukları. Ö d Aynı zamanda, söndürücü ile birlikte verilir sıcak suısıtma tankından e en az 60 sıcaklığa sahip va 0 İle birlikte. Kirecin söndürülmesi sırasında oluşan su buharı, bir su verme cihazı kullanılarak söndürücüden uzaklaştırılır. korsanlık ile ama-teknik kurulum.
Sönmemiş kireç parçalarını çıkarmak için kazanç eksikti de göz kısmı spiral şeklinde özel bir cihazla donatılmıştır. H e dopal, emiciden konveyöre, ardından sınıflandırıldığı ızgaraya çıkarılır. Parçalar, 70 mm'den daha büyük bir çapa sahip olan, bantlı konveyör boyunca ızgaradan aşağıya düşmedi. içinde büyük bir nedopalın sığınak akümülatöründe lyayutsya. Kaçırılan parçalar, bir pop büyüklüğünde e 70 mm'den küçük nehir kanalı, ızgaradan küçük depolama bunkerine düşüyor e dopala ve kamyonla çıkarıldı.
Kireç söndürme aparatından elde edilen kireç sütü özel bir kaba akar. ve al sınıflandırıcı.
Sınıflandırıcıda kireç sütünün saflaştırılması fark nedeniyle gerçekleşir. spesifik yer çekimi, incelik C a (OH) 2 ve safsızlıkların varlığı.
Sınıflandırıcının gövdesi kaynaklı yarı silindiriktir. R biz eğimli bir çukuruz. Üstte kum boşaltmak içinİle birlikte Bu olukların bir kapağı var.
Spiral bir taşıma mekanizmasıdır ve çökelme bölgesinden boşaltmaya kadar geniş bir kum sınıfının karıştırılmasına hizmet eder. de açılır tavan. Katı fraksiyon, bir vida vasıtasıyla bir trana çıkarılır.İle birlikte kapıcı ve ardından kum haznesine. Alt kısım uygulama a eğimli kısmında ze'den olan rata sınıflandırma havzası R boşaltma kapağından önce dışkı çökeltisi, kumların dehidrasyonudur.
Sınıflandırıcıdan sonra hazırlanan kireç sütü alıcıya girer. e 16 m kapasiteli shalks (ara tanklar) 3 , hangi santrifüj pompa n e iki çift hidrosiklon, tüketilebilir karıştırıcılara (toplama tankları) pompalanır. gi'de d rosiklonlar, kireç sütünün daha iyi saflaştırılmasıdır. saflaştırılmış iskele hidroc'tan ko hakkında ve klonlar kollektör vasıtasıyla 400 m3 kapasiteli karıştırma tanklarına gönderilir. 3 (4 adet).
Hidrosiklonların tabanından gelen kirlilikler (kumlar)İle birlikte yönettiğim kumların tutulduğu elekler t konveyör boyunca kum depolama kutusuna ve hye'den arıtılmış süt d rosiklonlar ara tanklara girer.
Kireç sütü elde etme sürecinde, geri dönüştürülmüş su kullanılır. hakkında rai, tesisin boru hattından geliyor. Kireç söndürme için su ısıtma e dalgıç dağların aparatında stvlyayutsya e niya (APG).
Toplama tanklarında elde edilen ticari kireç sütü n 100 g/dm'den az olmayan merkezleme 3 sürekli santrifüj pompa içinde ancak halka boru hattına taşınır. Halka boru hattından bireysel dallara ben etsya resepsiyon ve s gaz temizleme tesislerinin sirkülasyon tanklarına kireç sütü.
Kireç söndürme aparatı silindirik bir tamburdur, vr a 4 rpm'den fazla olmayan bir hızda silindirler üzerinde yuvarlanma,İle birlikte 0,5 eğimli uçlu 0 kireç sütünün serbest bırakılması için. için merkezde d tambur kapağında aparat g'ye beslemek için bir oluğun yerleştirildiği bir delik var hakkında sıcak su, sıcaklık ile (6010) 0 C ve bana haber ver. İç kısım tüm uzunluk boyunca tambur bir kılavuz tabakasına sahiptir ve ny, helisel olarak 12'lik bir açıyla kurulur 0 silindir oluşturan tambura, bl a yükleme kısmına giren kirecin sürekli sıcak su ile temas etmesi nedeniyle en az 100 g/dm konsantrasyonda kireç sütü oluşturur 3 , e başına boşaltmak için tamburun ekseni boyunca yerleştirilir h bölümü.
KİREÇ SÖNDÜRME CİHAZI MALZEME DENGESİ
1.İlk veriler
1.1 Ana reaksiyon
CaO + H20 \u003d Ca (OH) 2 + Q (65.4 kJ)
1.2 Başlangıç malzemelerinin ve reaksiyon ürünlerinin karakterizasyonu
tablo 1
CaO |
H2O |
Ca(OH)2 |
|
Molekül ağırlığı, kg/kmol Yoğunluk, kg / dm 3 Porozite, % |
56 3,36 34-46 |
18 1,0 |
74 2,24 |
Su oranı: kireç-3.54
Kireç pütürlülüğü 60:80 mm
Kireç bileşimi:
CaO %86
CaCO3 %14 (toplam CaCO3 içeren safsızlıklar da dahildir ve kireçte olanlar)
Gelen kireç sıcaklığı: t 1 \u003d 50 0 С
Gelen su sıcaklığı: t 2 \u003d 60 0 С
Giden süt kireç sıcaklığı: t 3 \u003d 90 0 С
Kireç söndürme kapasitesi: 120 ton/gün
Kireç sütü çözeltisinin yoğunluğu: 1,2 kg/m 3
Atıkla birlikte kireç kaybı: ağırlığın %7'si düşürülmedi
Nedopalde (kuru madde) kireç sütü kaybı: ağırlığın %40'ı.
2. Malzeme hesaplaması
Hesaplama 1000 kg kireç için yapılır.
Söndürücü saatlik çıktı (kireç için)
G 1 = = = 5000 kg/saat
nerede Gr gaz performansı ve kireç buzağı, kg
bir günde 24 saat sayısı, h
CaO miktarı hammaddede:
G CaO = G1 * 0,86 = 5000 * 0,86 = 4300 kg
nerede G 1 emicinin saatlik çıktısı, kg/h
Kireçte 0.86 CaO içeriği (% olarak)
Böyle bir miktarda kireci söndürmek için su gereklidir:
G2 = kg
burada G CaO, CaO miktarıdır hammaddede, kg
M CaO molar kütle CaO, kg/mol
MH2O molar su kütlesi, kg/mol
Bu böyle bir miktar üretir Ca(OH)2
G Ca (OH) 2 === 1826.2 kg
nerede G2
MCa(OH)2
M CaO molar kütle CaO, kg/mol
Söndürmek için verilen su miktarı
G 2 \u003d G CaO * 3.5 = 4300 * 3.5 = 15050 kg
burada G CaO, CaO miktarıdır hammaddede, kg
Söndürmeden sonra kireç sütü çözeltisindeki su miktarı:
GH 2 O \u003d GH 2 O - G 2 - G Ca (OH) 2 = 15050 1382 1826.2 = 11841.8 kg
nerede G H2O - hammaddedeki su miktarı, kg
G2 - söndürme için verilen su miktarı, kg
GCa(OH)2 kireç sütü miktarı, kg
Underpal ile CaO Kaybı:
G p \u003d G CaO * 0,07 = 4300 * 0,07 = 301 kg
burada G CaO, CaO miktarıdır hammaddede, kg
0,07 kireç kaybı (ağırlıkça), % olarak
Hidratlı durumda, bu ize karşılık gelecektir. Ca (OH) 2'nin son miktarı:
G Ca (OH) 2 === 397,8 kg
nerede G p - CaO kaybı, kg
MCa(OH)2 kireç sütü molar kütlesi, kg/mol
M CaO molar kütle CaO, kg/mol
Bu,% 40'tır, bu nedenle kütle düşmedi:
G ref. ===994.4 kg
Söndürürken, belirli bir miktar su buharlaşır, onu belirtiriz. X .
Daha sonra, atık ayrıldığında çözeltide su vardı:
G H 2 O \u003d (11841.8 X) kg
Nedopal ile su uzaklaştırılır:
G H 2 O \u003d (11841,8 - X) * 0,07 \u003d (828,9 - 0,07 X) kg
Söndürücüden çıkan süspansiyonun bileşimi:
Ca (OH) 2 : G Ca (OH) 2 = 1826,2 397,8 = 1428.4 kg
H 2 O: G H 2 O \u003d (11841,8 X) (828,9 0,07 X) \u003d (11012.9 0,93 X) kg
Toplam: (12441.3 0.93 X ) kg
X ısı dengesi kullanılarak belirlenebilir: X \u003d 122,3 kg
Soğurucunun konsolide malzeme dengesi.
Tablo 2
Bileşenler |
Gelen |
Tüketim |
||||
nesne Ah evet |
Toplam |
gider kalemleri evet |
reaksiyon için |
pot e ri |
Toplam |
|
CaO |
4300 |
4300 |
4300 |
4300 |
||
H2O |
15050 |
15050 |
1382 |
10899 |
942,64 |
13223,64 |
Ca(OH)2 |
1428,4 |
397,8 |
1826,2 |
|||
Toplam |
19350 |
19350 |
KİREÇ SÖNDÜRME CİHAZI ISI DENGESİ
1. Isının gelişi
1.1. Kireç ile:
KJ,
burada kJ / kg * derece CaO'nun ısı kapasitesidir.
1.2. Ekzotermik bir reaksiyondan:
Q p \u003d 65,4 kJ / mol CaO
kJ.
1.3. Su ile:
KJ.
1.4. Çözünme ısısı:
kJ,
nerede kJ / mol çözünme ısısı Ca(OH)2.
kJ
2. Isı tüketimi
2.1. süspansiyon ile :
a) Ca (OH) 2 çökeltisi ile
kJ,
nerede kJ / kg*deg tortunun ısı kapasitesi Ca(OH)2
B) "kireç sütü" çözeltisi ile
KJ,
burada kJ / kg * derece "kireç sütü" süspansiyonunun ısı kapasitesidir
KJ
2.2. avuç içi ile
kJ /kg*derece özısı eksik;
90'da suyun kJ /kg entalpisi 0C;
KJ
2.3. Su buharı ile:
Neresi 90'da kJ /kg buhar entalpisi 0C;
KJ
2.4. Isı kaybı çevre:
3 J
nerede - ısı transfer katsayısı, W / m 2 * derece;
F emici yan yüzey, m 2 ;
Soğurucu duvar ve ortam havası arasındaki sıcaklık gradyanı sen ev;
Saatten saniyeye dönüştürme faktörü.
Soğurucu duvarın sıcaklığını 50'ye eşit alıyoruz 0 C, ortam sıcaklığı besleme havası 20 0 С.
-.
Söndürücü boyutları (kabul edin):
mm
M2
W / m 2 * dolu
3 \u003d 77472,45 kJ
kJ
Isı dengesi denkleminden
4385214.9 kJ = (4180198,87 + 231.39 X ) kJ
Neresi:
Kilogram
Ardından, buharlaşmadan sonra çözelti şunları içerir:
- su 11841.6-88 = 11753.6 kg, 815.84 kg nedopalli su ve 10937.76 kg süspansiyonlu su dahil.
Söndürücünün konsolide ısı dengesi.
Tablo 3
Gelen |
Tüketim |
||||
Madde |
kJ |
Madde |
kJ |
||
kireç ile |
170925 |
3,3 |
süspansiyonlu |
3683842,45 |
84 |
Su ile |
3774540 |
86 |
avuç içi ile |
389908 |
8,89 |
Ekzotermik bir reaksiyondan |
403940,3 |
9,28 |
su buharı ile |
233992 |
5,34 |
Çözeltinin ısısı Ca(OH) 2 |
35809,6 |
0,82 |
Isı kaybı |
77472,45 |
1,77 |
Toplam |
4385214,9 |
100 |
Toplam |
4385214,9 |
100 |
KİREÇ SÖNDÜRME CİHAZININ YAPISAL HESAPLAMASI
- İlk veri:
Saatlik verimlilik: G 1 \u003d 5000 kg / sa (CaO)
G 2 \u003d 15050 kg / sa (H 2 O)
Tambur açısı: α = 0,5 0
tambur çapı: Db = 2,2 m
Tambur devir sayısı: n = 3 ÷ 4 rpm (kabul et)
Doldurma faktörü: φ = 0.248 (kabul et)
Malzeme Yoğunluğu:
nerede X 1 \u003d 0,07 ağırlık duruma göre, alt kısımdaki CaO miktarı
Kg/dm3 kireç söndürme tamburundaki malzeme yoğunluğu
- Kireç söndürücü tamburunun tahmini uzunluğu:
nerede Q = tambur çapına bağlı olarak 0,6 katsayı;
n = 3 ÷ 4 rpm = rpm tamburun saniyedeki devir sayısı.
Tamburda malzeme kalma süresi:
*φ,
nerede v b davul hacmi,
g cf tamburdan geçen ortalama malzeme kütlesi, kg/s
Kireç sütünün hazırlanmasında kullanılan söndürücülerin tambur boyu 12 ila 15 m, çapları ise 1,8 ila 2,5 m, yani. boyutları ile damper tambur hacmi:
min D b = 1.8 m, L b = 12 m,
maks D b = 2,5 m, L b = 15 m
m3'e eşit
Tamburdan geçen ortalama malzeme kütlesi:
kg/s
Malzemenin söndürücüde kalma süresi:
İTİBAREN.
Ardından, tamburun uzunluğu:
- n = 0.05 rpm'de
L b \u003d 0,6 * 0,05 * 2,2 * 7443.6 * tg 0,5 \u003d 4,3 m
- n = 0.067 rpm'de
L b \u003d 0.6 * 0.067 * 2.2 * 7443.6 * tg 0.5 \u003d 5.75 m
Çizime göre, kireç söndürücü tamburunun uzunluğu 8,5 m'dir ve bu, söndüğü için kabul edilebilirdir. ve işletme koşullarına göre, operatör büyük kireç topakları ile çalışacak ve hakkında mecazi olarak söndürme süresini artırın.
- Soğurucu tamburu döndürmek için gereken güç:
* φ ,
burada A=k 1 *k 2 *k 3 ,
1 =1 tambur çapı katsayısı ( Db ≤ 2,2 m);
k2 \u003d Tamburun dolum derecesini ve su yoğunluğunu dikkate alarak 1 katsayı emekli maaşından;
k3 \u003d kireç parçalarının boyutunu dikkate alarak 1.1 katsayısı;
n tamburun devir sayısı, rpm.
\u003d 0,95 verimlilik motor (kabul et)
kW
ÇÖZÜM
Söndürme aparatı aşağıdaki teknik özelliklere sahiptir.
Bir çeşit |
AI-2.2 |
Toplu beslemeye göreCaO, t/gün |
120 |
Dönme frekansı, min-1 |
3-4 |
redüktör |
1TsGU-250-40-21U1 |
boyutlar, mm |
|
tambur çapı |
1800 |
tambur uzunluğu |
8500 |
elektrik motoru |
|
güç, kWt |
7,5 |
Dönme frekansı, min-1 |
1000 |
Yapılan hesaplamalara göre söndürme aparatının yeterli olduğu sonucuna varılabilir.eüretimde kabul edilen norm ve standartları oluşturur ve ayrılmaz bir parçasıdır.akireç sütü üretiminde stu.
KAYNAKÇA
- Zaitsev I.D., Tkach G.A., Stoev N.D. Soda üretimi. M.: "Xvemia" 1986
- İnorganik maddelerin teknolojisi ile ilgili hesaplamalar. Altında. ed. P. V. Dybina, M.: “Daha yüksek. okul" 1967
- K.F. Pavlov, P.G. Romankov, A.A. Noskov "Süresindeki örnekler ve görevlerİle birliktebaykuşlar ve kimyasal teknolojinin aparatları”. M.: "Kimya", 1976
- Anuryev V.I. Tasarımcı makine üreticisinin el kitabı. Cilt 1. M.: "Malastik endüstrisi" 1999
- Tabunshchikov N.P. Kireç üretimi. M.: "Xvemia" 1974
- Monastyrev A. V. Kireç üretimi. M.: Stroyizdat, 1972
- ÜZERİNDE. Koluzin, V.N. Sokolov, A.Ya. Shapiro "Kurs için örnekler ve görevlerdefabrikalar kimyasal endüstri". M. L.: "Mühendislik", 1966
- OLARAK. Krivorot "Makine ve aparat tasarımının tasarımı ve temelleri" xvetaklit sanayi". M.: "Mühendislik", 1976
- Çalışma talimatları Kireç söndürme operatörü: RI-38-006-2002, OJSC AVISMA.
Buluş şeker endüstrisi, özellikle şeker içeren çözeltilerin kireç-karbon dioksit saflaştırma teknolojisi ile ilgilidir. Yöntem, ağırlıkça 100 oranında su ile kireci söndürmeyi içerir. 105-115 wt.h'ye kadar kireç kireç, bir kireç macunu oluşturmak üzere tamamen hidrate olana kadar su, daha sonra soğutulur ve 40-55°C sıcaklıkta difüzyon suyu ile karıştırılır. Kireç sütü, titreşimli bir elek ve hidrosiklonlar üzerinde sönmemiş parçacıklardan temizlenir. Titreşimli bir elek üzerinde ayrılan sönmemiş partiküller, ağırlıkça %1-5 oranında yanmış kireç miktarında su ile yıkanır ve elde edilen yıkama, hidrosiklonlara beslenen kireç sütü ile karıştırılır. ETKİ: Buluş, kireç sütünün hazırlanması sırasında şeker ayrışmasının önlenmesini sağlar ve kireç sütünün kalitesini iyileştirir. 1 hasta.
2332467 sayılı RF patentine ait çizimler
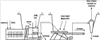
Buluş şeker endüstrisi, özellikle şeker içeren çözeltilerin kireç-karbon dioksit saflaştırma teknolojisi ile ilgilidir.
80-95 °C sıcaklığa sahip su ile ağırlıkça 100 wt.h oranında söndürme kireci dahil olmak üzere, şeker içeren çözeltilerin saflaştırılması için kireç sütü elde etmek için bilinen bir yöntem. kireç ve 80-100 wt.h. hav oluşana kadar su, 80-95 °C'ye soğutulması ve belirli bir miktarda su ile karıştırılması, belirli bir yoğunlukta kireç sütü elde edilinceye kadar 60-85 °C sıcaklıkta.
Bilinen yöntemin dezavantajları: kullanım Büyük bir sayı saf su kireç sütünün hazırlanması ve yeterince yüksek aktiviteye sahip olmayan kireç sütü elde edilmesi için.
Önerilen yöntemin en yakın analogu, şeker içeren çözeltilerin saflaştırılması için kireç sütü elde etme yöntemi olup, kirecin 80-95 °C sıcaklığa sahip su ile ağırlıkça 100 oranında söndürülmesini içerir. kireç ve 62-100 wt.h. gevşek bir yığın kütle oluşana kadar su, ardından soğutulur, bir süspansiyon elde etmek için,% 0,5-15 sakaroz içeriğine ve 60-85 ° C sıcaklığa sahip şeker içeren bir çözelti (yıkar, dökülür) eklenir gevşek yığın kütleye dönüştürülür ve işlem 80-85°C'ye kadar soğutularak gerçekleştirilir ve elde edilen süspansiyon, safsızlıklardan arındırılır.
Bilinen yöntemin dezavantajı, sönmüş kireçle karıştırmak için kullanılan şeker çözeltilerinde bulunan sakarozun bir kısmının zararlı madde girişi ile ayrışmasına yol açan, yeterince yüksek derecede kireç sökme sağlamamasıdır. şeker üretimi sakarozun saflaştırılmış meyve suyuna ayrışma ürünleri ve bu şeker içeren çözeltilerin 60-85°C sıcaklıkta kullanılması, yeterince yüksek aktiviteye sahip kireç sütü sağlamaz.
Buluşun teknik sonucu, kireç sütünün hazırlanması sırasında şekerin bozunmasını önlemek ve kireç sütünün kalitesini iyileştirmektir.
Teknik sonuç, şeker içeren çözeltilerin saflaştırılması için kireç sütü elde etme yönteminin, kireci suyla karıştırarak söndürmeyi, sönmüş kireci soğutmayı, şeker içeren bir çözeltiyle karıştırmayı ve sütü saflaştırmayı içermesi gerçeğiyle elde edilir. Titreşimli bir elek ve hidrosiklonlar üzerinde sönmemiş parçacıklardan kireç. Ayrıca kireç ve su ağırlıkça 100 wt.h oranında kullanılmaktadır. kireç ve 105-115 wt.h. su ve işlem bir kireç macunu oluşana kadar gerçekleştirilir, 40-55 ° C sıcaklıktaki difüzyon suyu sönmüş kireç ile karıştırmak için şeker içeren çözeltilerden kullanılırken, sönmemiş parçacıklar arıtma sırasında titreşimli bir elek üzerinde ayrılır. Kireç sütü ağırlıkça % 1-5 yanmış kireç miktarında su ile yıkanır ve elde edilen yıkama hidrosiklonlara beslenen kireç sütü ile karıştırılır.
Buluş, işlem diyagramını gösteren çizimde gösterilmektedir.
Şeker içeren çözeltilerin saflaştırılması için kireç sütü elde etme yöntemi aşağıdaki gibi gerçekleştirilir. Kireç söndürücüde (1) söndürülmeden önce, sönmemiş kireç 80-95 °C sıcaklıktaki su ile ağırlıkça 100 oranında karıştırılır. kireç ve 105-115 wt.h. su ve 10-20 dakika karıştırılarak kirecin tamamen sönmesi ve kireç hamurunun oluşması için yeterlidir. Karıştırma sırasında, kireç macunu 100°C'den fazla bir sıcaklığa ısıtılır, ardından 80-95°C'ye soğutulur. Elde edilen kireç macunu, şekerin termal ayrışması olmadan gerçekleşen büyük sönmemiş parçacıkları ayırmak için bir elek ile donatılmış bir karıştırıcı 2 içinde 40-55 ° C sıcaklıkta %10-15 sakaroz içeren difüzyon suyu ile karıştırılır. kireç kabartmasının aksine kireç hamurunda az miktarda sönmemiş CaO parçacıkları. Ayrıca mikserde 40-55 °C sıcaklıktaki 2 difüzyon suyunu kireç macunu ile karıştırırken, sönmemiş 8-10 mm boyutundaki partiküller ayrıştırılır ve uygun koşullar Karıştırma için sağlanan meyve suyu daha fazla olduğundan, söndürme sırasında oluşan Ca(OH)2'nin çözünürlüğü için düşük sıcaklık bilinen yönteme göre; bu sıcaklık, şeker pancarı yongalarından sakarozun ekstraksiyonu sırasında difüzyon aparatından çıkan meyve suyunun olağan sıcaklığından kaynaklanmaktadır. Böylece istenilen yoğunlukta 1,16-1,22 g/cm3 süt elde edilir.
Elde edilen kireç sütü, yanmış kireç ağırlığının %1-5'i oranında suyla yıkanan sönmemiş parçacıklardan bir titreşimli elek (3) üzerinde saflaştırmaya tabi tutulur ve elde edilen yıkama, kireç sütü ile karıştırılır. Bu, orta fraksiyonun sönmemiş parçacıklarını ayırmak için kireç ve sakaroz sütünün parçacıklardan yıkanmasını mümkün kılar. Bu şekilde elde edilen kireç sütü hidrosiklonlarda 4 temizlendikten sonra şeker içeren çözeltilerin saflaştırılmasına alınır.
Örnek 1. Yoğunluğu 1.16 g/cm3 olan şeker çözeltilerinin saflaştırılması için kireç sütü alın. Bunu yapmak için 311 g sönmemiş kireç, 80°C sıcaklığa sahip 326.5 g su ile ağırlıkça 100 saat oranında karıştırılarak söndürülür. kireç ve 105 wt.h. su, karışımı soğuturken 10 dakika karıştırarak Akar su gömlek aracılığıyla. Ortaya çıkan 85 °C sıcaklığa sahip kireç macunu, %13,8 şeker, %16,7 katı madde içeren difüzyon suyu ile 40 °C sıcaklıkta 960 g oranında seyreltilir, 10 g miktarında su ile yıkanır. ve elde edilen yıkama kireç sütüne eklenir. Ayrıca, elde edilen 1.16 g/cm3 yoğunluğa sahip kireç sütü süspansiyonu, 0.14 MPa'lık bir basınçta bir laboratuvar hidrosiklonunda safsızlıklardan arındırılır.
Taze hazırlanmış saf kireç sütünde şeker içeriği, sönmemiş safsızlıklar, kireç sütünün aktivitesi belirlenir ve titreşimli eleklerden sonra yıkamada CaO içeriği belirlenir. Böylece, 311 g CaO'dan elde edilen ve% 13,8 şeker,% 16,7 katı içeren difüzyon suyu ile seyreltilmiş 1,6 litre kireç sütündeki sakaroz içeriği, 40 ° C sıcaklıkta 131,2 g olarak gerçekleşti. kireç sütünün hazırlanmasında ağırlıkça %0.7-0.8 olmuştur. Taze hazırlanmış saflaştırılmış kireç sütündeki safsızlıkların içeriği 14 g/l idi. Titreşimli elek yıkayıcıdaki CaO içeriği 2.1 g, kireç sütünün etkinliği ise %89'du.
Örnek 2. İşlemi gerçekleştirin bilinen yol. Yoğunluğu 1.16 g/cm3 olan şeker içeren çözeltilerin saflaştırılması için kireç sütü hazırlanır. Bunu yapmak için, 311 g kireç, 80°C sıcaklığa sahip 193 g su ile ağırlıkça 100 wt.h oranında söndürülür. kireç ve 62 wt.h. su, 10 dakika karıştırılır, 80 ° C'ye soğutulur, daha sonra elde edilen kabarık kireç, karışımın soğutulması sırasında% 13,8 şeker,% 16,7 katı, 60 ° C'lik bir sıcaklıkta difüzyon suyu ile seyreltilir, karışım soğutulur 85 °C'ye kadar. Elde edilen süspansiyon, titreşimli bir elek üzerinde sönmemiş parçacıklardan arındırmaya tabi tutulur, 0,2 mm'lik bir boyuta ezilir ve kireç sütüne geri döndürülür. Elde edilen 1.16 g/cm3 yoğunluğa sahip kireç sütü süspansiyonu, 0.14 MPa'lık bir basınçta bir laboratuvar hidrosiklonunda safsızlıklardan arındırılır. Taze hazırlanmış saflaştırılmış kireç sütünde şeker içeriği, sönmemiş safsızlıklar, kireç sütünün aktivitesi belirlenir ve ezilmiş sönmemiş partiküllerde aktif CaO belirlenir.
Böylece, 311 g CaO'dan elde edilen ve % 13,8 şeker içeren difüzyon suyu ile seyreltilmiş 1,8 litre kireç sütündeki sakaroz içeriği, 40 ° C sıcaklıkta% 16,7 katı madde, 166.3 g olarak gerçekleşti. kireç sütünün hazırlanmasında ağırlıkça %2,9 olmuştur. Taze hazırlanmış saflaştırılmış kireç sütündeki safsızlıkların içeriği 34.2 g/L idi. Kireç sütünün aktivitesi %83 idi.
Prototip ile elde edilen kireç sütünün yoğunluğu ve ayrıca önerilen yöntemle 1.16 g/cm3, ancak kireç sütünün kalite göstergeleri daha düşüktü. Böylece, kireç sütünün saflaştırılmasında kırma kullanımı nedeniyle saflaştırılmış kireç sütündeki safsızlıkların içeriği 2 kat arttı, kireç sütünün hazırlanmasında sükroz kaybı 3 kat daha fazla oldu ve aktivite daha düşüktü. %6.
İDDİA
Kireç sütünün su ile karıştırılarak söndürülmesini, sönmüş kirecin soğutulmasını, şeker içeren bir çözelti ile karıştırılmasını ve titreşimli bir elek üzerinde sönmemiş parçacıklardan kireç sütünün arıtılmasını içeren, şeker içeren çözeltileri temizlemek için kireç sütü üretme yöntemi ve hidrosiklonlar, kireç ve suyun ağırlıkça 100 oranında kullanılmasıyla karakterize edilir. kireç ve 105-115 wt.h. su ve işlem bir kireç macunu oluşana kadar gerçekleştirilir, 40-55 ° C sıcaklıktaki difüzyon suyu sönmüş kireç ile karıştırmak için şeker içeren çözeltilerden kullanılırken, sönmemiş parçacıklar arıtma sırasında titreşimli bir elek üzerinde ayrılır. Kireç sütü ağırlıkça % 1-5 yanmış kireç miktarında su ile yıkanır ve elde edilen yıkama hidrosiklonlara beslenen kireç sütü ile karıştırılır.